En ce moment je fais un truc à gauche et un autre à droite , en fait je termine ce que je n'ai pas voulu faire avant et tout ces petits détails me prennent un temps fou , mais j'aperçois le bout de la voie .......
Bon là maintenant je vais attaquer le système de freinage .
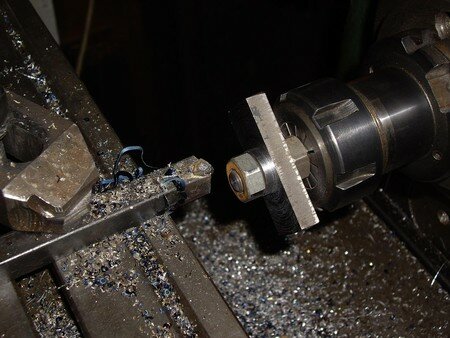
Les paliers sont fait dans un barreau de 12x20 mm . Ils sont montés sur une vis M10 puis serrés en pince pour le tournage de la partie cylindrique .
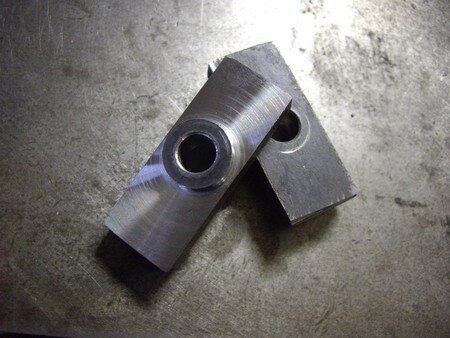
Je commence par tourner le diamètre 19 sur 4 mm de profondeur .
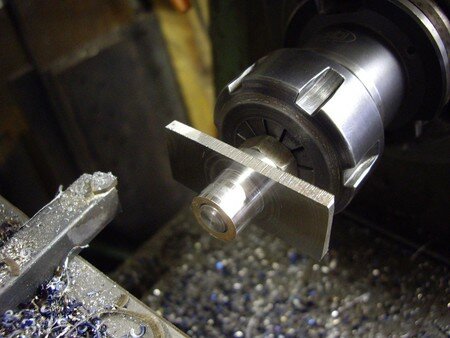
Puis je fais le diamètres 15 mm qui aura raison de l'écrou se bloquage .
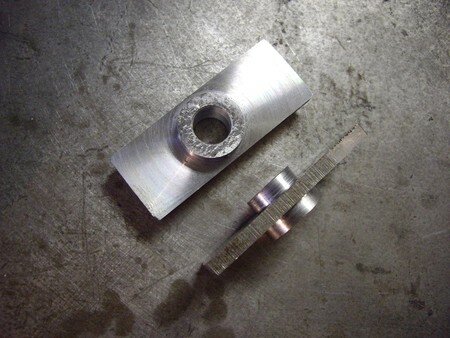
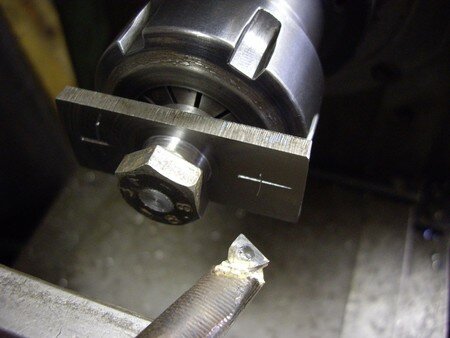
Je trace les axes de perçage avec la pointe d'un outil qui est réglé à la hauteur de l'axe .
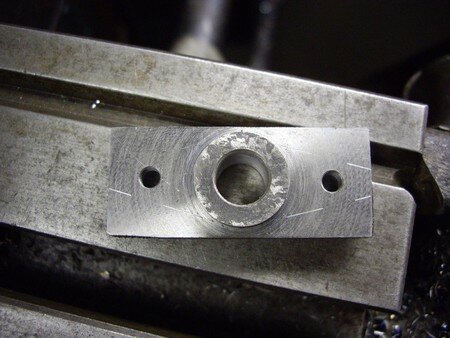
Ce sont des têtes de vis qui ont servi de guide pour le tracage du contour extérieur .
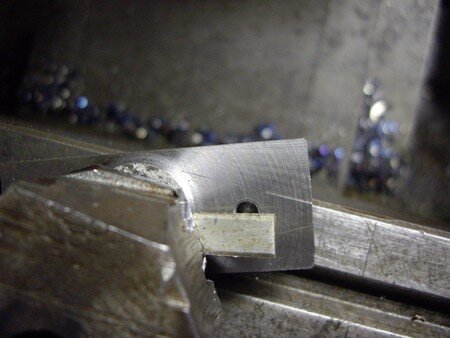
La pièce est positionnée bien dans l'axe de la fraiseuse en suivant le tracé .
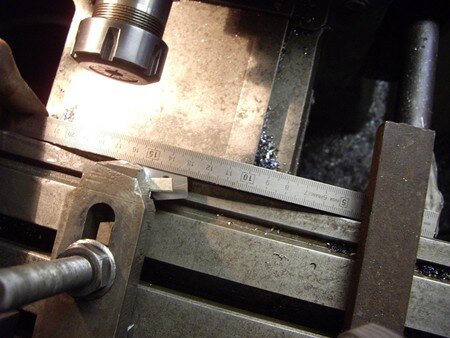
C'est un réglet qui est plaqué contre le bord de la table qui me sert de guide pour positionner les pièces .
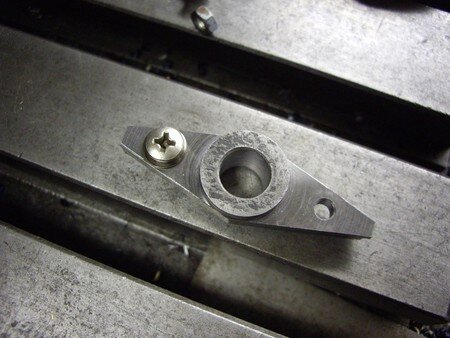
Voici le début de l'ébauche des pièces .
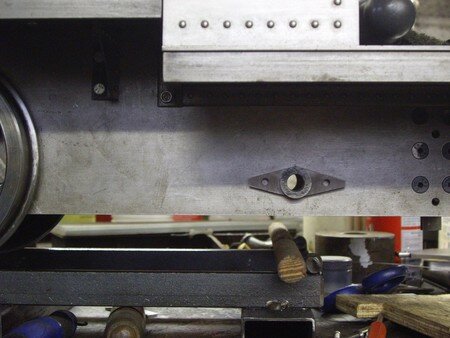
Une petite mise en place avant même que cela soit fini pour se rendre compte de l'allure .
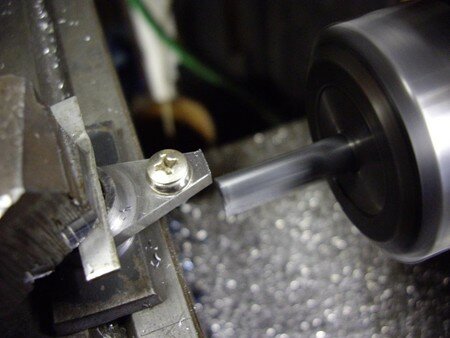
L'extrémité est fraisée en s'approchant le plus possible de la tête de vis .
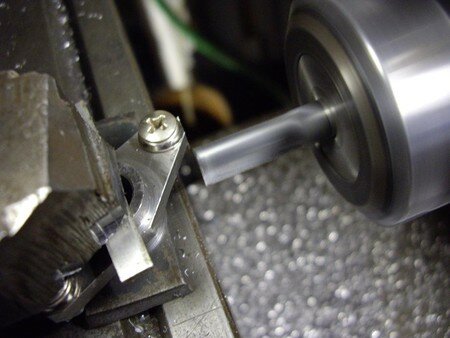
La même chose mais en biais .
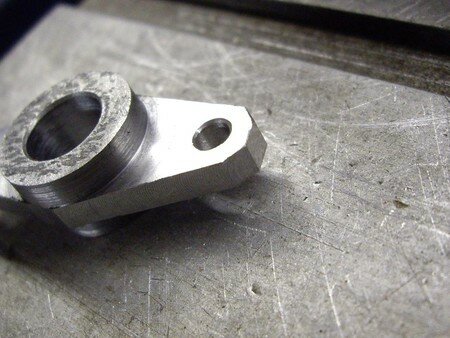
Il reste à donner un coups de lapidaire pour casser les angles ....
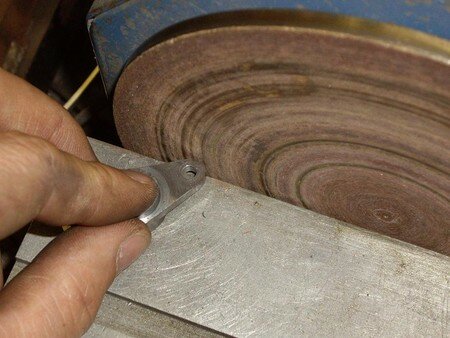
.....sans se brûler les doigts !
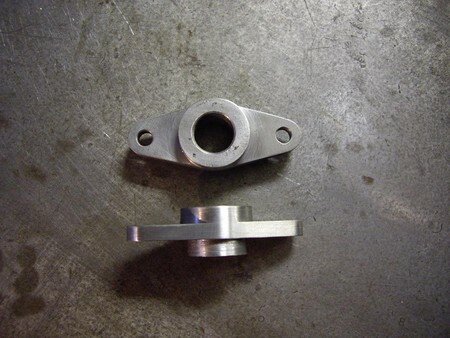
Et hop , deux jolis paliers .
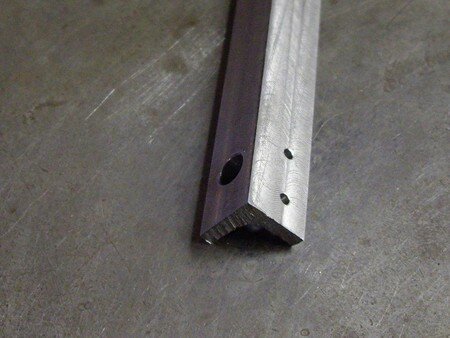
Le guide de l'axe de manoeuvre est réalisé à partir d'une cornière de 15x15 qui est fraisée au bonnes côtes .
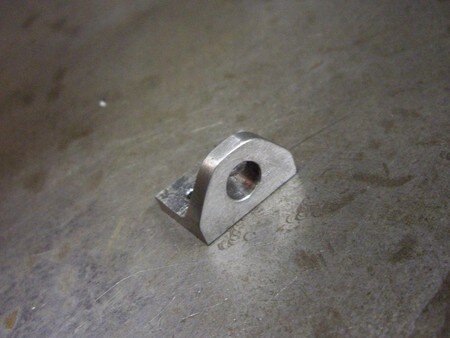
Et après deux trois opérations voici à quoi cela ressemble .
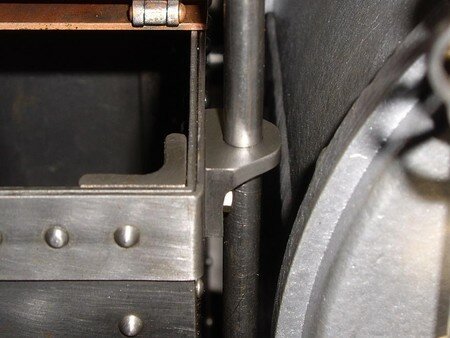
Le voici en place .
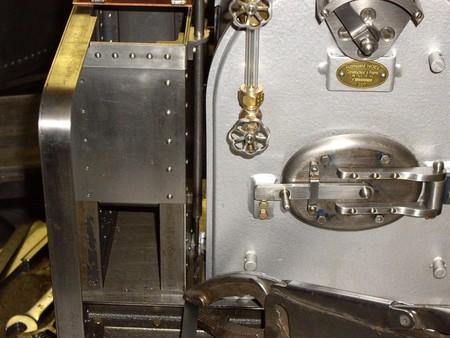
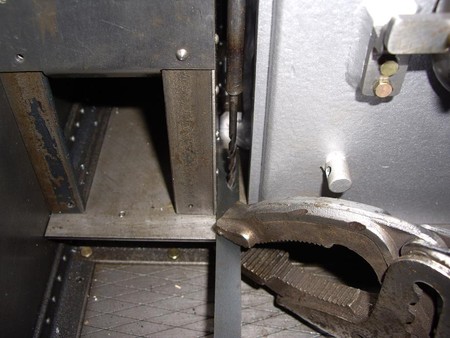
Pour percer le planché j'ai utilisé un forêt monté sur une tige de 6 mm et guidé par une chute percée placée aux bonnes côtes de positionnement .
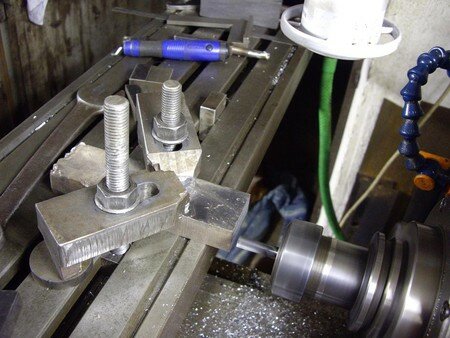
Sous le plancher , il y a un palier pour le guidage de l'axe de manoeuvre et au début c'est un bloc de 20 mm d'épaisseur .
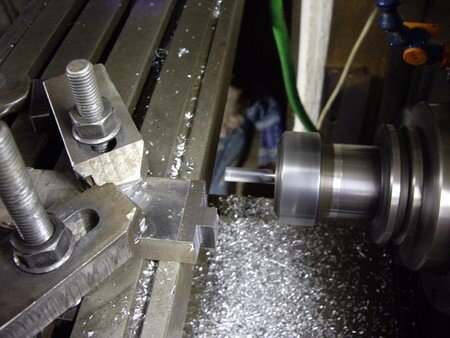
La première opération consiste à faire deux épaulements .
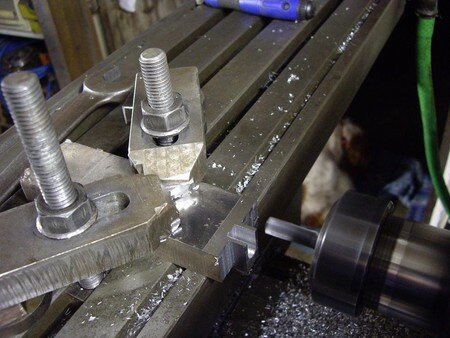
Ensuite je fais un rainurage de 8 mm puis la pièce est sciée du bloc .
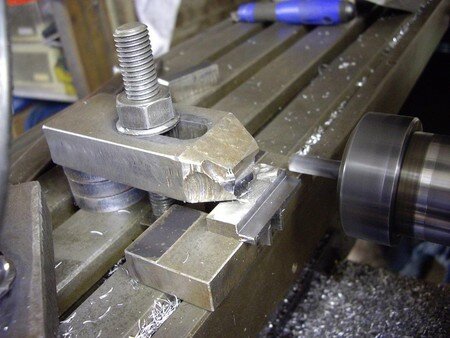
J'aurais pu scier un peut plus près du tracé , ah , quand on aime les copeaux tous les prétextes sont bons pour en faire !
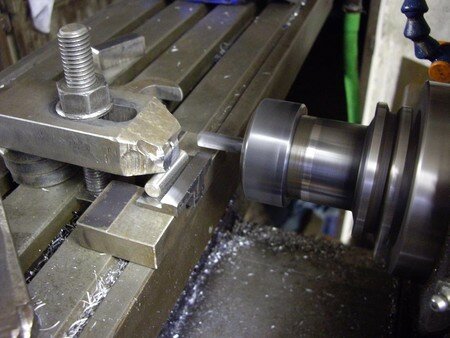
Donc , la pièce est mise à l'épaisseur en deux opérations avec retournement .
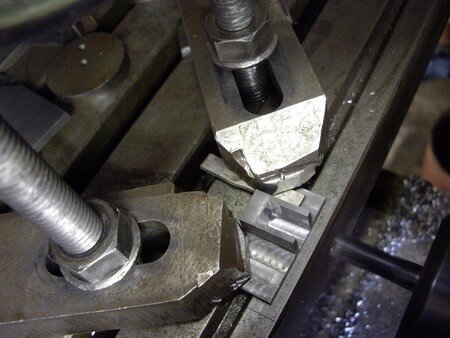
La rainure de 8 est finie avec un fond plat dans l'autre sens .
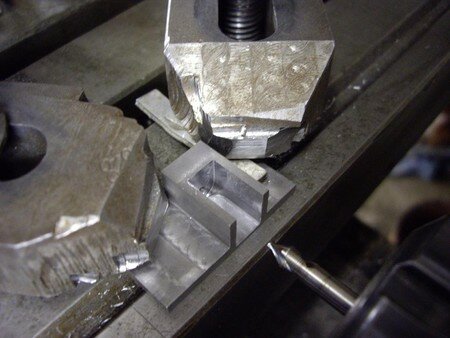
Le trou de l'axe est pointé précisément .
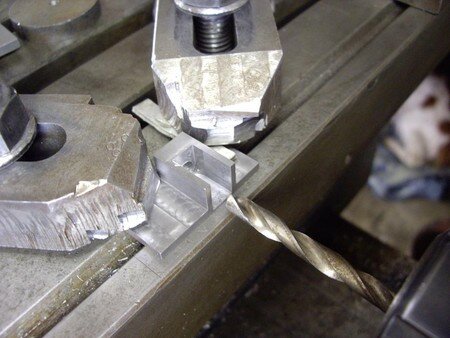
Ensuite il est percé à 6 mm .
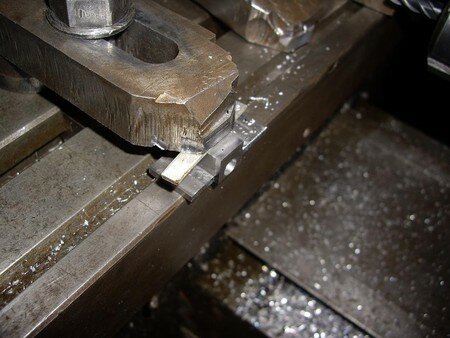
La mise en forme des oreilles de fixation est faite en suivant le tacé .
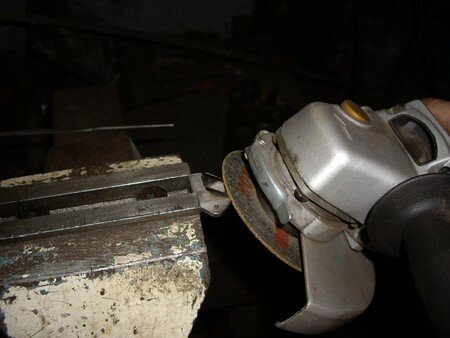
Les pans coupés sont tronçonnés au disque de 1.6 mm d'épaisseur pour plus de finesse dans la coupe .
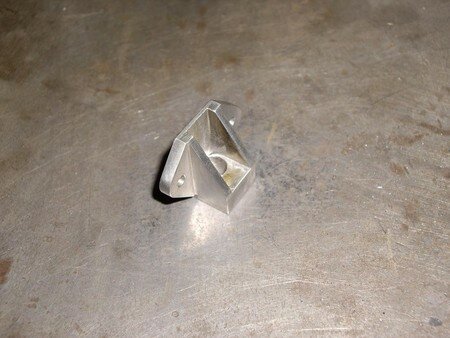
Le palier est fini .

Et là il prend place .
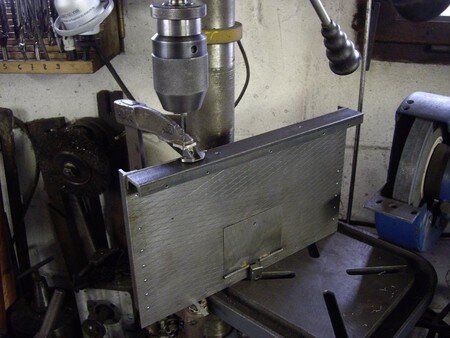
Un serre-joint maintien le palier en place pendant le contre perçage .
Le guide de noix .
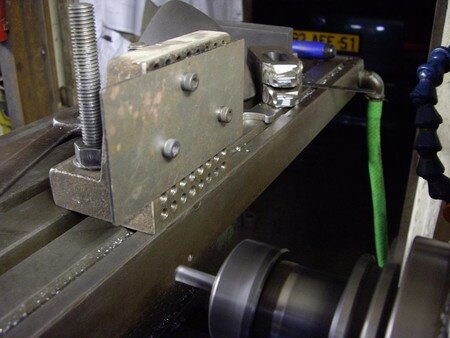
Un support en fer plat est réalisé pour guider la noix et qu'elle ne fasse pas des tours sur elle même pendant que la fourche de commande est levée par l'action du frein pneumatique .
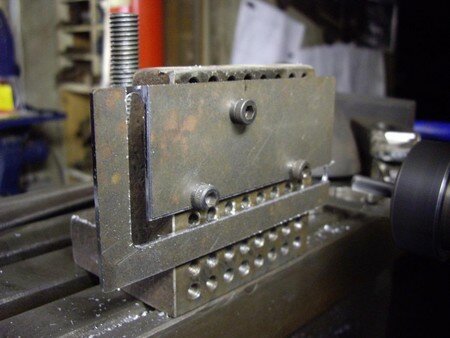
Cette pièce en forme d'équerre est fraisée dans de la tôle de 2 mm serrée sur un montage . Je laisse des points d'attache aux extrémités qui seront facilement éliminés à la lime .
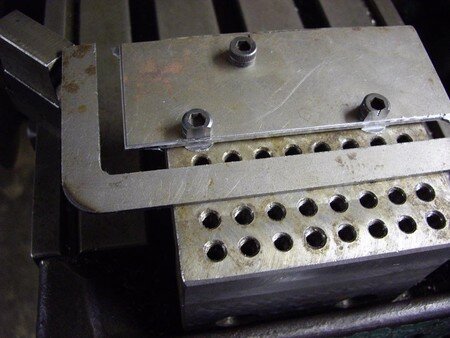
J'ai encore mal calculé mon coup et ce sont les vis qui ont trinquées . J'avais intercalé des rondelles entre la pièce et le support de façon à ne pas faire de marques dedans .
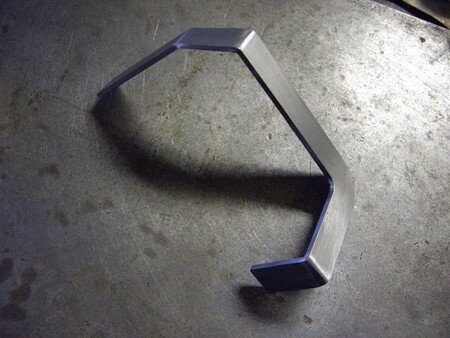
Le plus compliqué c'est d'avoir les bonnes côtes de pliage à la fin .
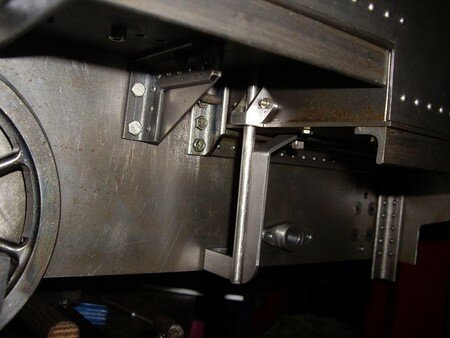
Montage à blanc du guide pour voir .
La noix .
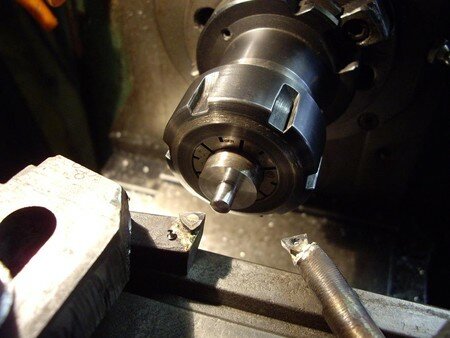
Elle est tournée dans du rond de 18 mm .Je commence par faire un épaulement de 6 mm plus long que nécessaire pour pouvoir reprendre la pièce par la suite .
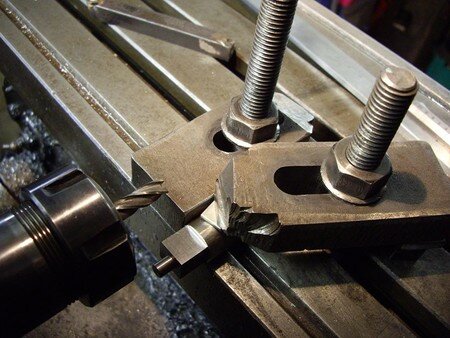
Le carré de 12 mm est fraisé .
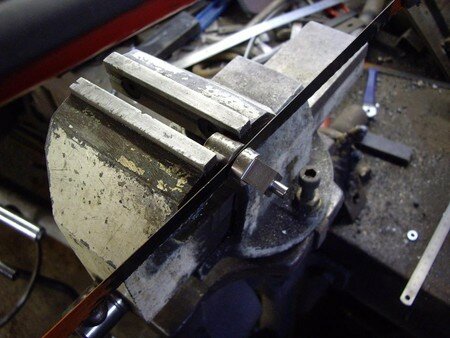
La pièce est sciée à longueur.
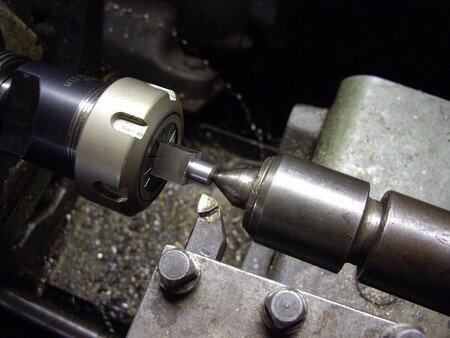
Je fais une reprise en montage mixte car le porte à faux est trop important pour une opération d'ébauche .
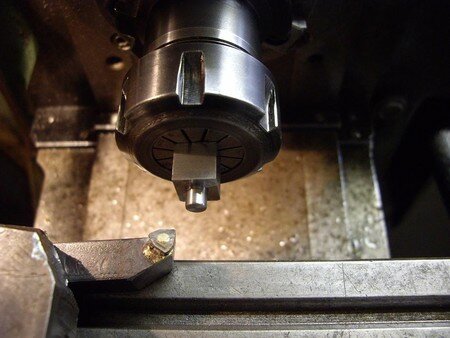
La finition de la longueur est faite sur la fraiseuse .
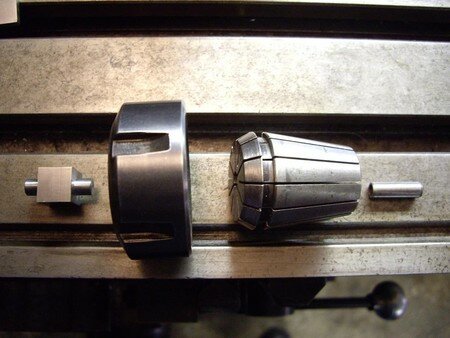
Quand je serre en pince une pièce de faible longueur je met en extrémité intérieur de la pince une goupille sur une portée de 3 mm , comme elle est du même diamètre que l'axe le serrage est bien parallèle et plus efficace .
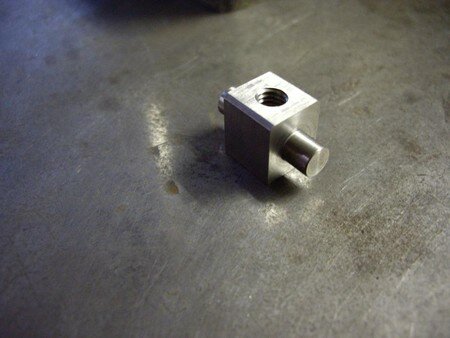
La noix finie.
L'axe de commande .
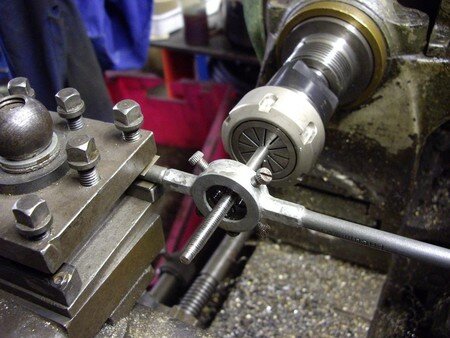
Il est fileté M6 sur 70 mm de long . Le porte filière est serré dans le porte outil pour avoir un guidage bien dans l'axe et ne pas avoir un filetage qui part en S .
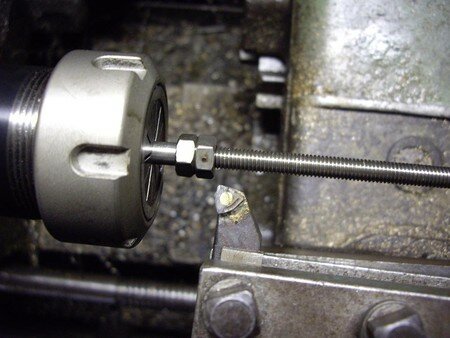
Deux butées sont faite à partir d'écrous M6 qui sont contre serrés pendant le tournage.
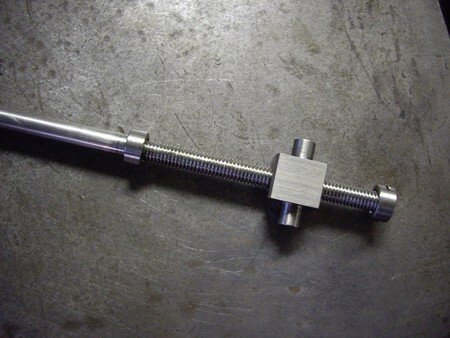
La butée de gauche est collée au blocpress et celle de droite est bloquée par une goupille fendue .
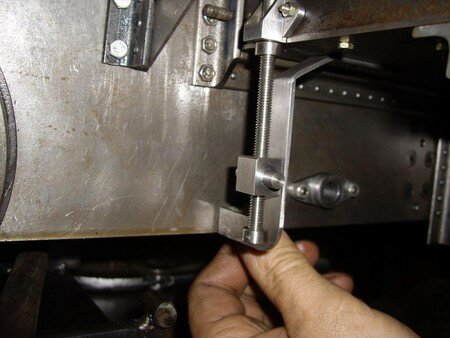
Une présentation des pièces les une par rapport aux autres .
La manivelle de frein .
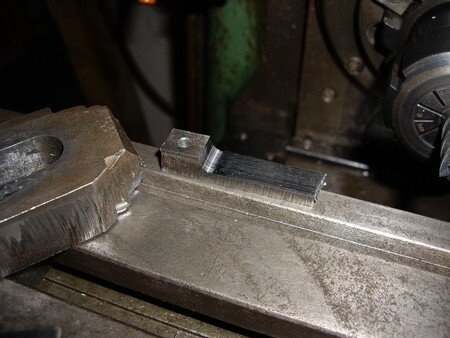
Elle est ébauchée dans du carré de 8x8 mm .
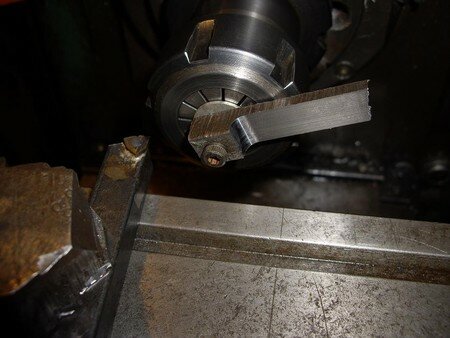
La partie cylindrique est tournée en prenant soin de ne pas usiner la partie fraisée qui est déjà à la bonne côte . De cette façon on limite les risques de vibration .
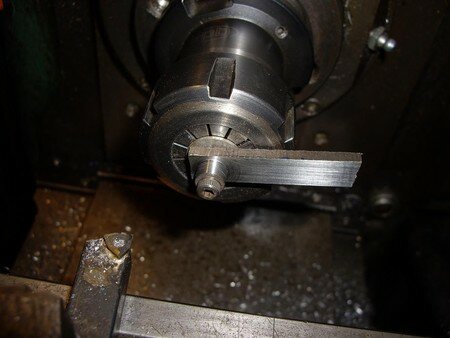
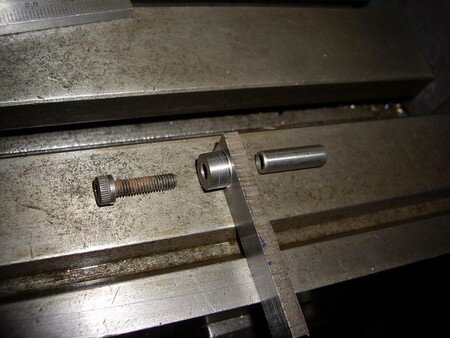
Me montage d'usinage est fait à partir d'une goupille taraudée M4 .
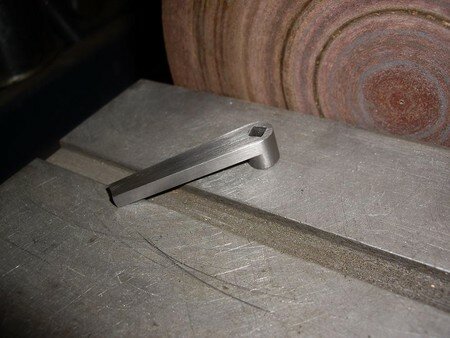
L'empeinte carrée est faire avec une queue de taraud HS .
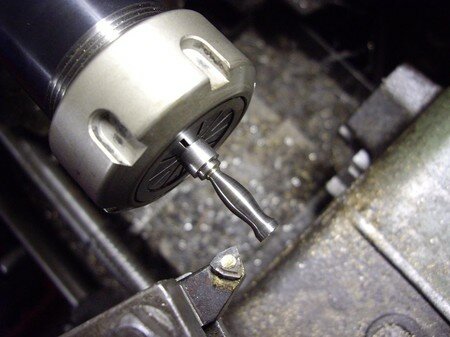
La poignée est tournée à la vollée en suivant l'inspiration du moment .
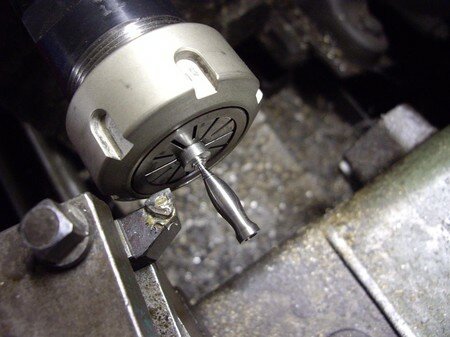
La pointe est affinée au maximum pour faciliter la séparation . Elle est taraudée M4 pour vissage sur le levier .
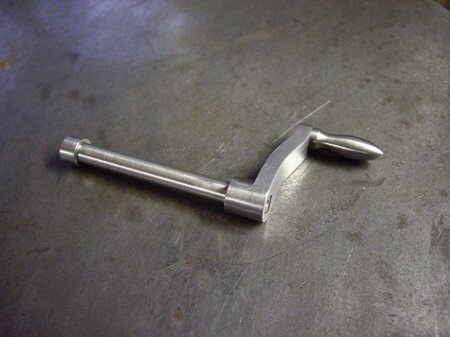
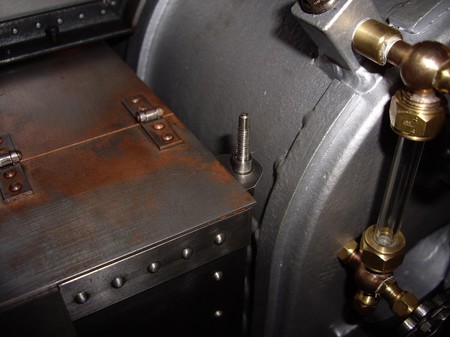
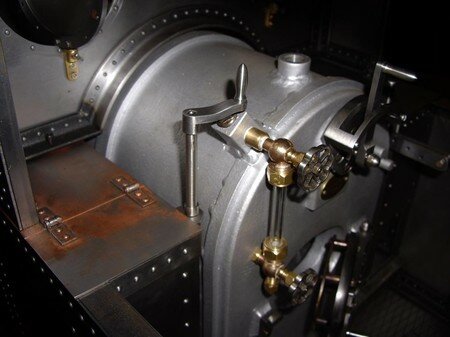
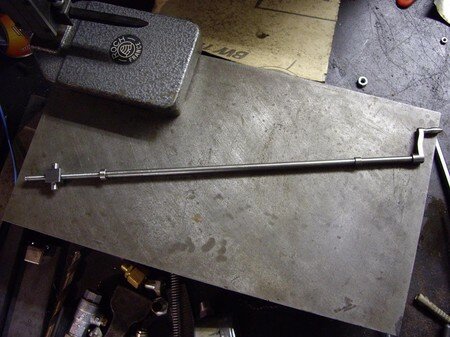
Je vous propose un intermède avec cette vidéo de tournage ( inox de 8 mm )
La fourche de commande .
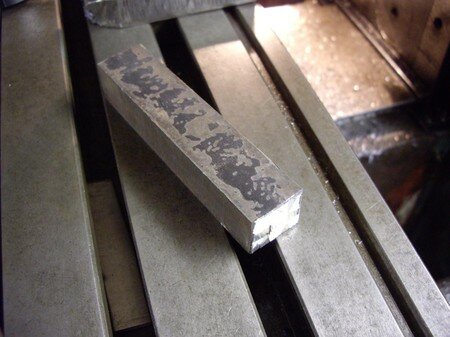
Au départ il y a un barreau de 22x20x100.
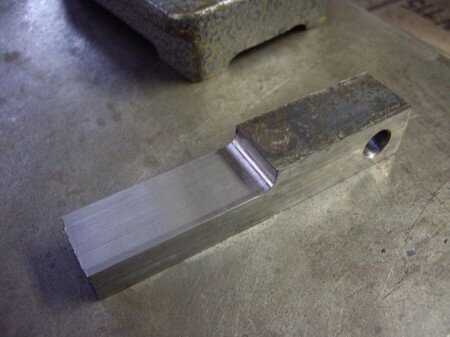
je commence par dresser 3 faces et percer le trou de 10 mm , ensuite je fraise une plage qui sera le point de départ de l'arrondi de la fourchette .
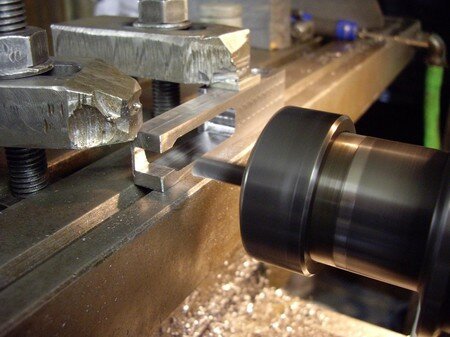
La fourchette est fraisée en laissant un point d'attache pour ne pas que les deux pattes vibres .
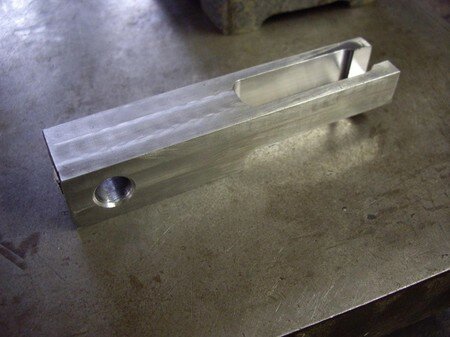
L'ouverture des deux pattes fait 12.5 mm .
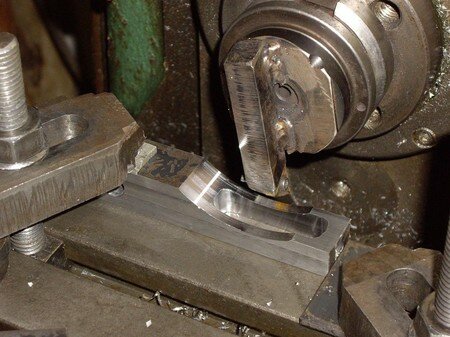
L'arrondi est fait avec une fraise qui à un rayon qui ressemble à ce que je veux . On voit bien le point d'attache qui est encore en place sur la pièce .
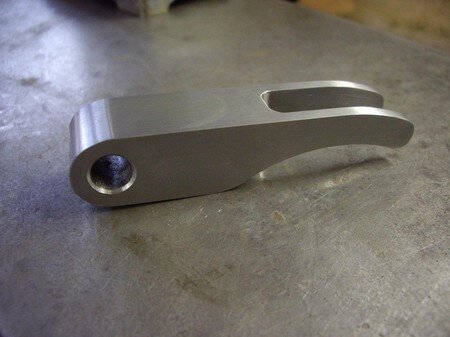
Il reste à faire le taraudage de la vis pointeau pour le bloquage sur l'axe .
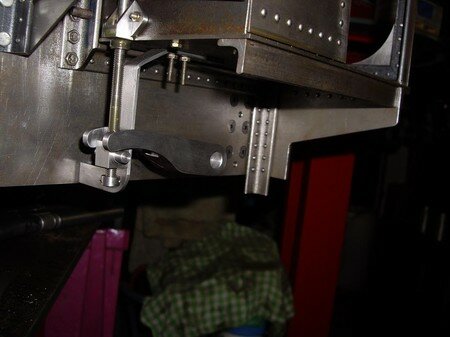
Et voila la fourche de commande en place.
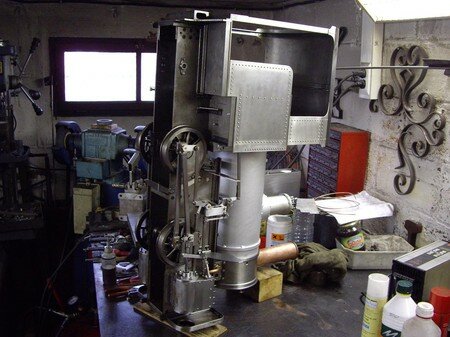
La loco fait un petit séjour sur le museau le temps que je bricole les freins en dessous .
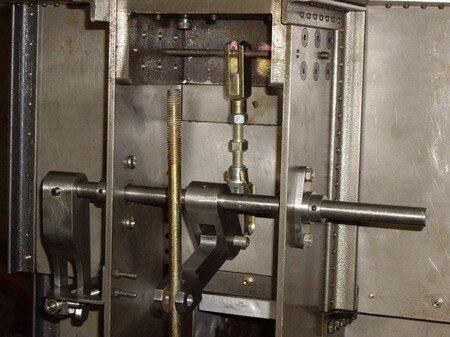
J'ai fais un renvoi de timonerie qui permet de régler facilement le frein avec un tendeur du commerce ( plutôt de récup ! ) avec un pas à gauche et un autre à droite .
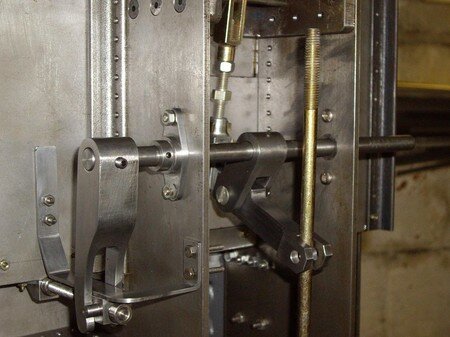
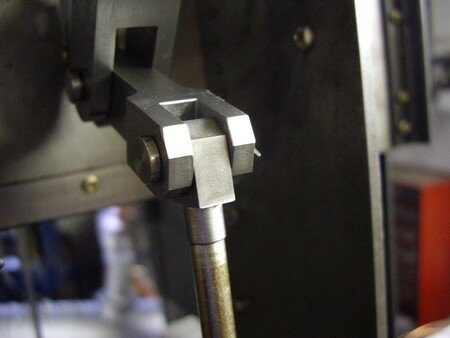
Un oeuillet tout simple est vissé à l'extrémité de la tige de timonerie du frein .
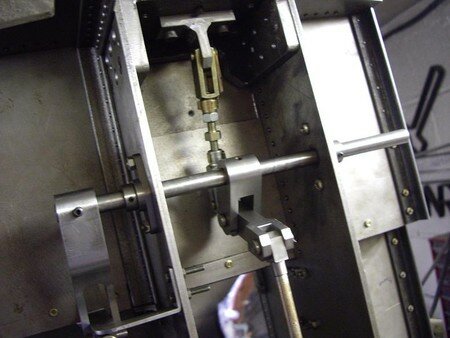
Une vue de l'ensemble de la commande de renvoi du frein .
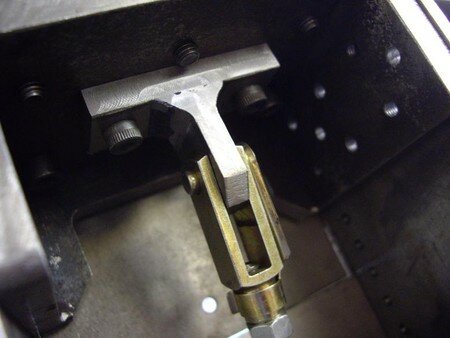
L'ancrage arrière est fait dans du fer plat de 20x8 soudé en Té puis usiné pour calibrage .
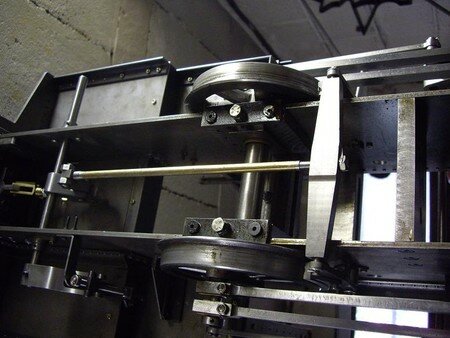
La tige de timonerie et tournée au diamètre 6 aux extrémités puis fileté M6.
Les sabots de frein.
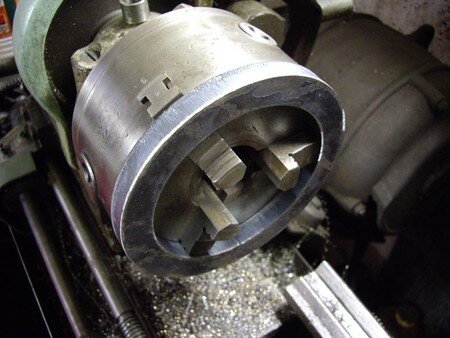
Pour faire des sabots je pars d'une bride diamètre 163 mm en épaisseur 15 mm.
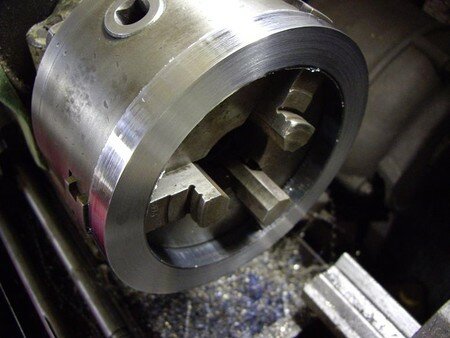
Tournage et dressage des premières faces.
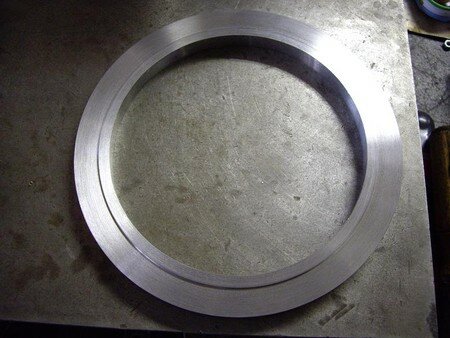
Le diamètre central est tourné conique pour s'ajuster au bandage de la roue . L'épaisseur finale de la bride est de 12 mm au plus large et de 10 mm au niveau de l'épaulement .
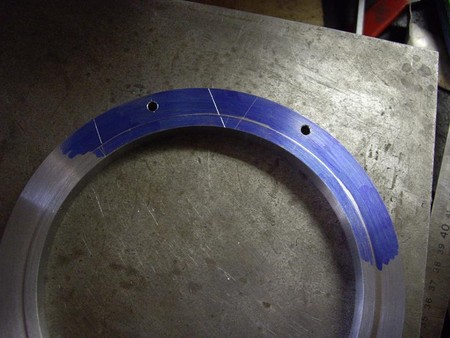
Traçage de la longueur du sabot et perçage du trou de maintien.
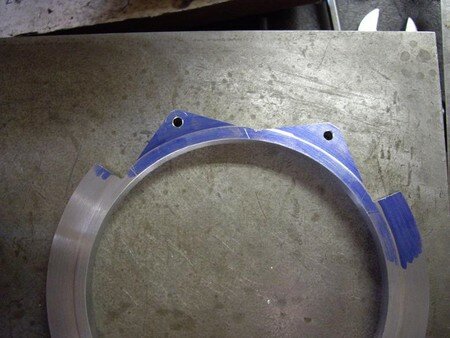
Le profil extérieur est tracé puis fraisé en suivant le trait.
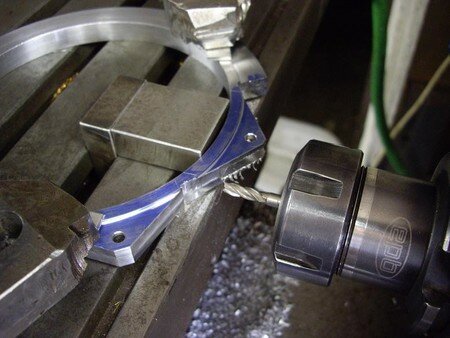
La pièce est centrée sur une cale pour fraiser la rainure de 4.5 mm de large dans le sens de la longueur.
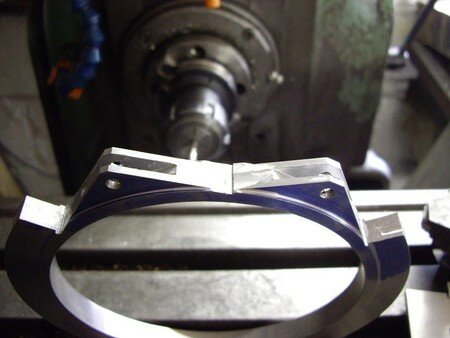
Les deux pièces sont presque terminées , il reste juste à les scier et fraiser les extrémités puis faire l'arrondis au lapidaire.
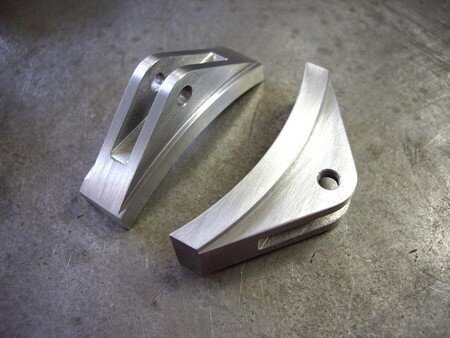
Voici deux sabots de frein prêts à être monté , si un jour ils arrivent à la cote d'usure (ce qui n'arrivera certainement jamais !) il reste assez de place sur la bride pour en refaire une paire .
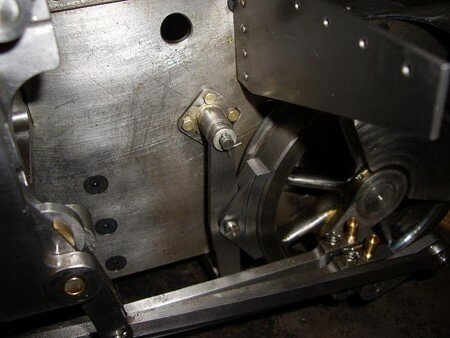
Le voila monté .