Nous allons maintenant passer à la réalisation du système de freinage des bogies .
Ce dispositif ne servira que quand la machine sera à l'arrêt car le freinage dynamique sera effectué par la régulation des moteurs électriques .
Je commence par les quatre cylindres de frein .
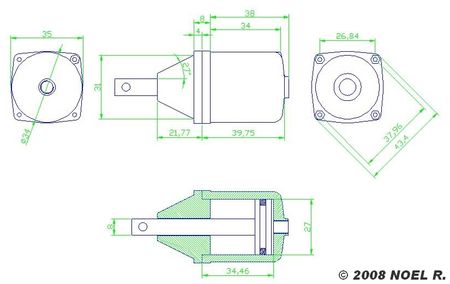
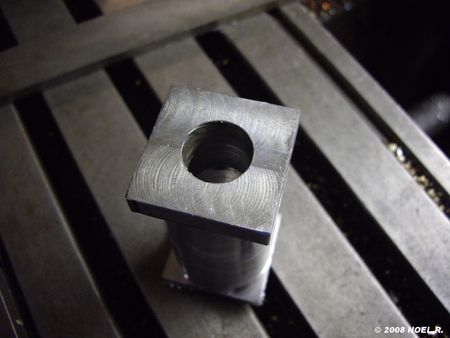
Les pièces sont faites dans du carré de 37x37 de longueur 80 mm . En premier il est percé à une extrémité un trou de diamètre 18 mm et à l'autre un centre pour la pointe tournante du tour . Ces deux opérations sont faites sur la perceuse à colonne .
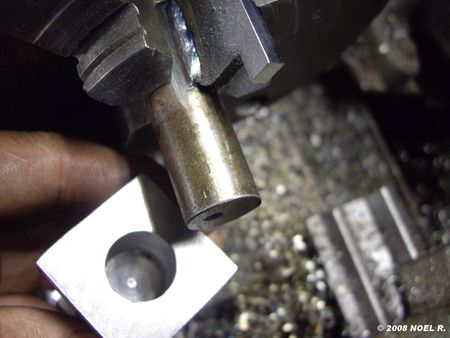
La pièce va être reprise en tournage entre ce rond de 18 et la pointe tournante . l'entraînement se fait par le carré .
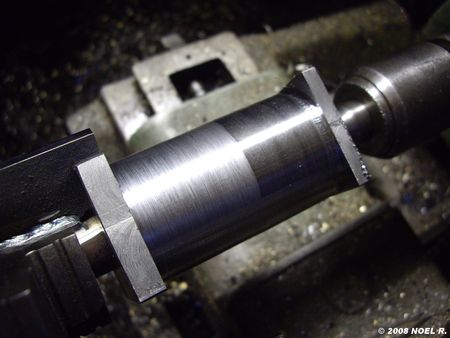
La partie centrale est tournée au diamètre 37 mm .
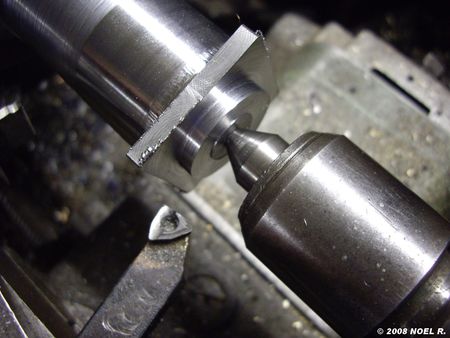
Un épaulement est fait sur 4 mm de long au diamètre 27 mm .
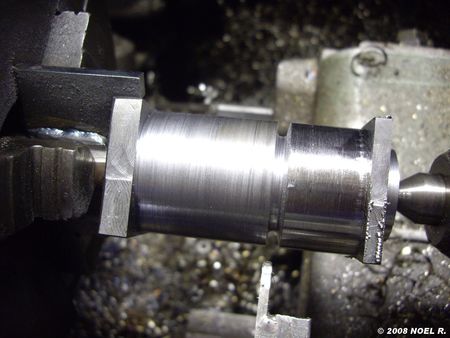
Une saignée est réalisée à 30 mm du bord pour délimiter les deux pièces .

La partie droite qui est le nez du cylindre est tournée au diamètre 31 mm et la partie carrée est amenée à une épaisseur de 4 mm .
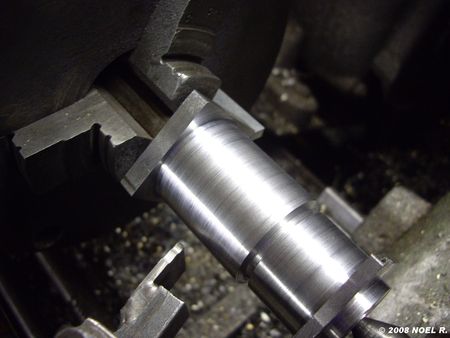
La partie de gauche qui forme le corps du cylindre est tournée au diamètre 34 mm .
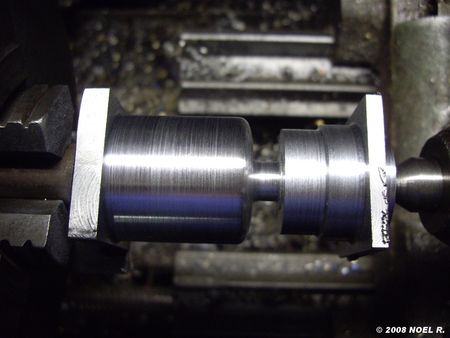
Le corps du cylindre est mis à sa forme définitive et la partie centrale est réduite au diamètre 10,5 mm .
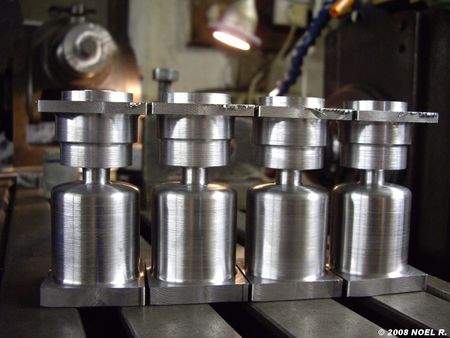
C'est une façon peu commune pour faire ces pièces mais c'est comme cela que je procède sans mandrin à quatre mors .
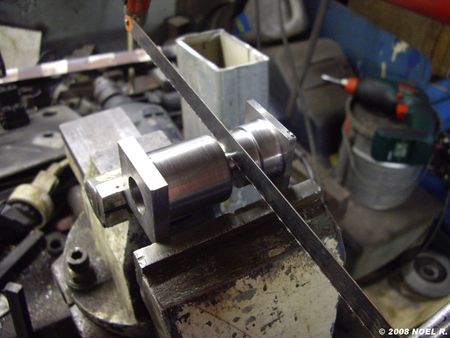
Pour séparer les deux pièces il n'y a que le diamètre 10,5 mm à scier !
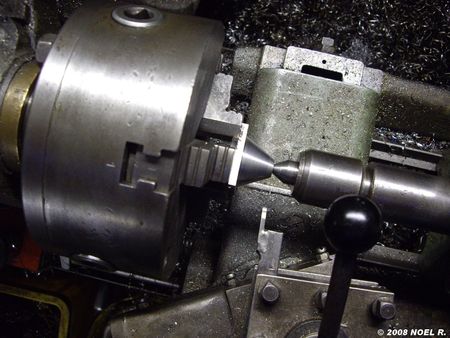
Reprise du nez de cylindre pour le tourner conique .
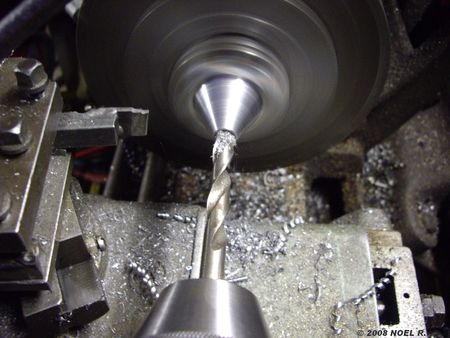
Percage du trou central pour la tige de verin .
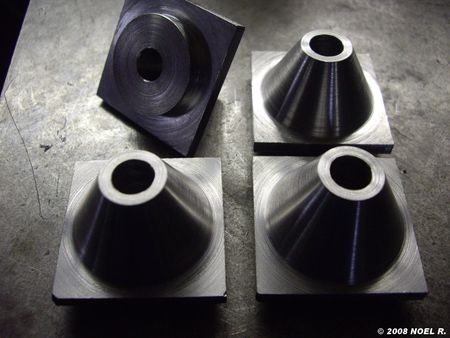
Les pièces sont terminés .
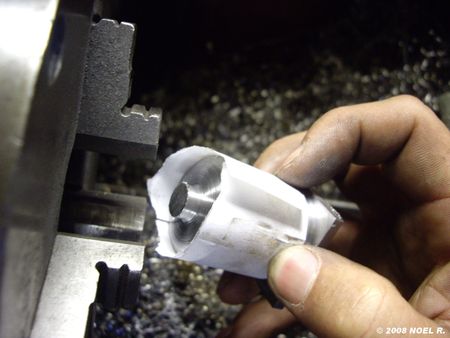
Pour l'usinage de l'alésage du corps du cylindre je vais mettre un morceau de papier entre les mors et la pièce pour ne pas la marquer .
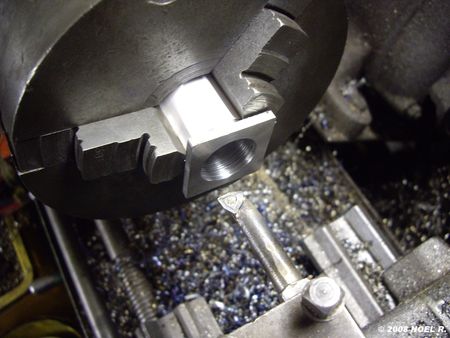
Les corps de cylindre sont alésés au diamètre 27 mm sur une profondeur de 35 mm .
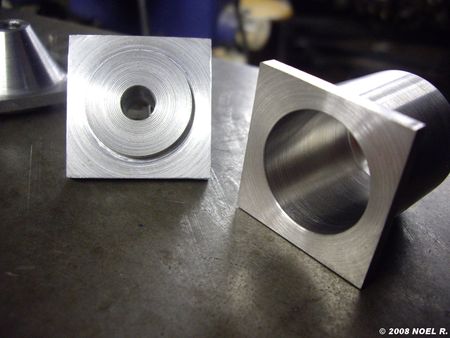
La pièce terminée il ne reste que 3,5 mm d'épaisseur .

Montage à blanc pour voir l'allure générale de l'ensemble .
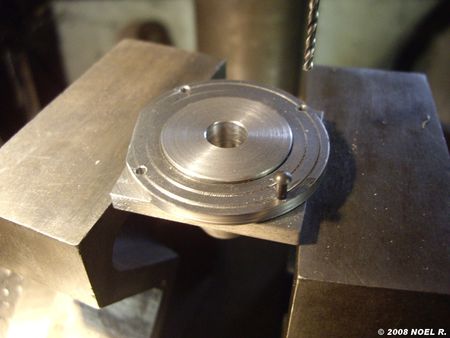
Les percage des tous de fixation sont fait avec l'aide d'un gabarit .Le plat à gauche n'a rien à voir , c'est simplement que la chute était trop petite ! ou pas assez grande .....
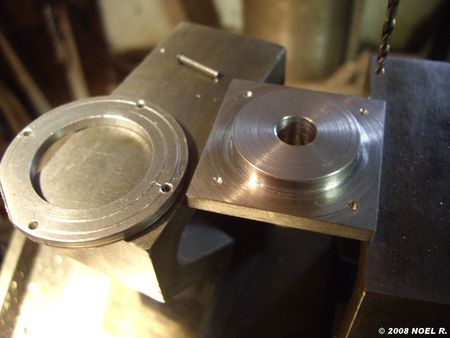
Le premier trou est percé complètement pour y mettre un rond de 2 mm qui va tenir le gabarit en place pendant le pointage des autres trous .
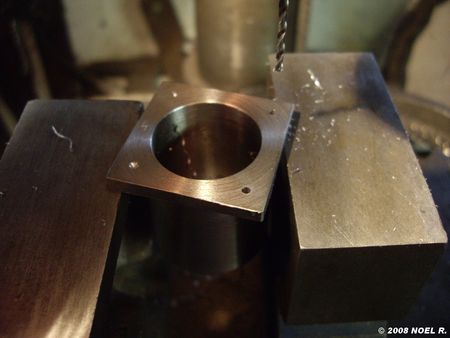
Le corps du verin a été contre-pointé avec la pièce précédente . Toujours en mettant un axe dans le premier trou pour le guidage angulaire .
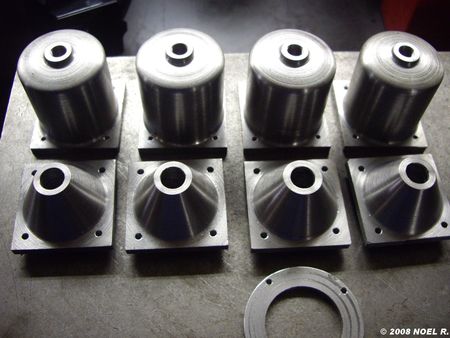
Les nez de verin sont percés à leur diamètre final de 2,5 mm et les coprs seront taraudés à M2,5 .
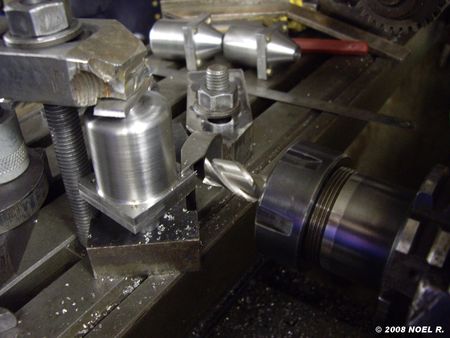
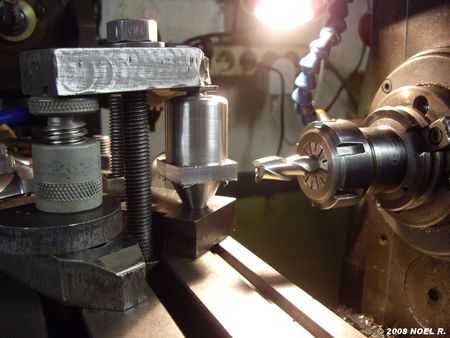
Fraisage de la collerette pour faire deux pentes .
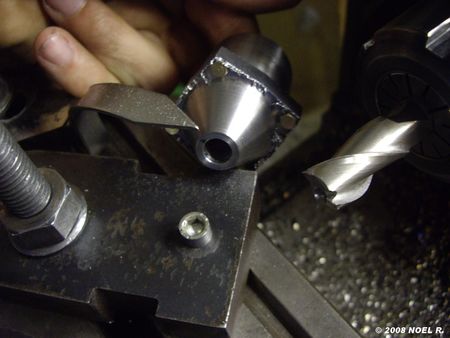
La pièces est centrée sur une vis dont la tête a été usinée au diamètre du trou du nez de verin .
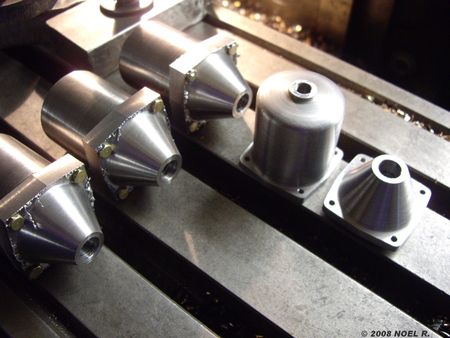
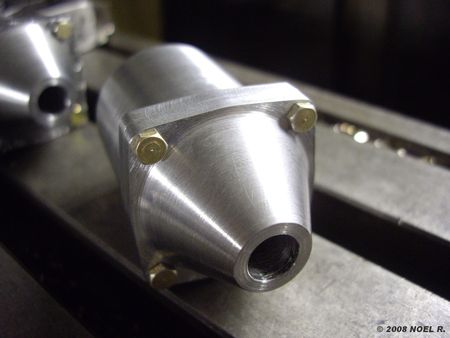
Les angles sont arrondis à la lime .
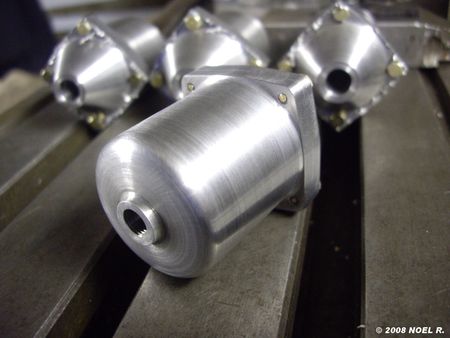
Le trou de l'alimentation en air est taraudé à 1/4x40 .
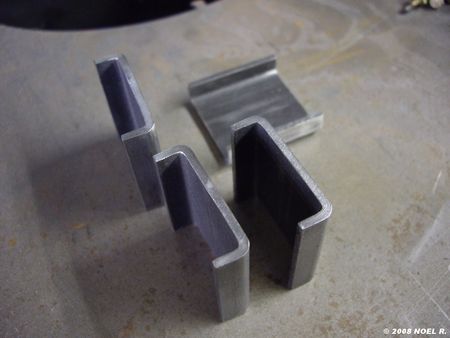
Des supports sont découpés dans du tube carré de 30x30 et seront pointés au corps du verin pour créer une assise plane .
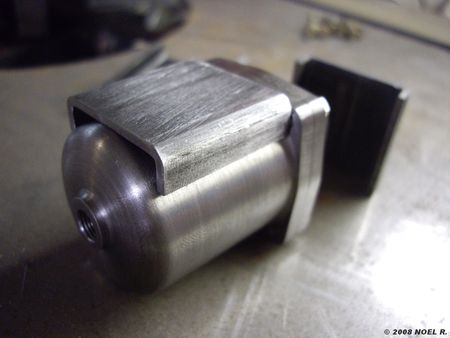
Voici le support en place .
La Decauville est sortie brûler du charbon avec des copines à Barnac début Juin et vous pouvez voir les photos ici
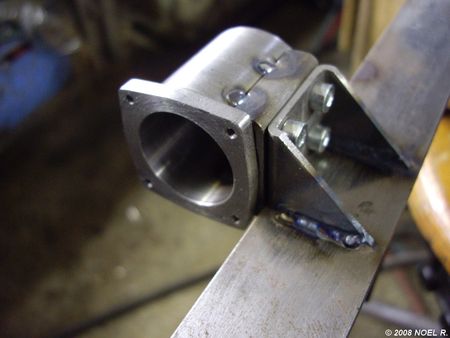
Une platine faite dans un morceau de tube carré est soudée sur le bogie pour supporter le cylindre.
Les supports de balancier de frein .
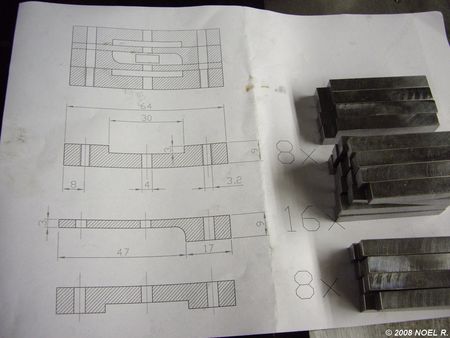
Les balanciers de frein pour les sabots intérieurs du bogie sont supportés par des biellettes qui sont maintenues par les pièces que nous allons réaliser maintenant . Au départ il faut faire des barreaux de 9x9 mm .
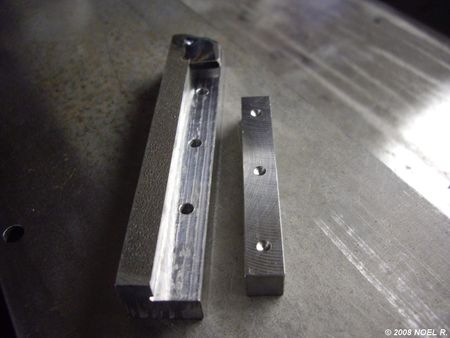
Afin de faire les perçage identiques sur toutes les pièces , je fais un montage qui me sert à pointer les trous .
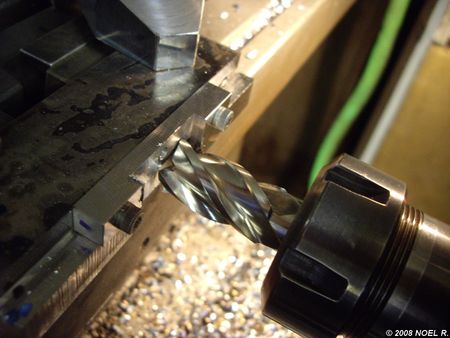
Les pièces sont fixées à travers ces trous pour la phase de fraisage de l'évidement cental .
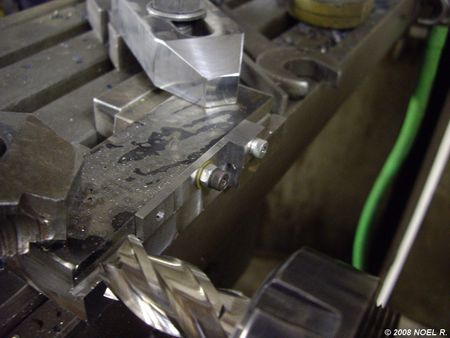
Sur une partie des pièces l'épaulement est prolongé sur le bout.
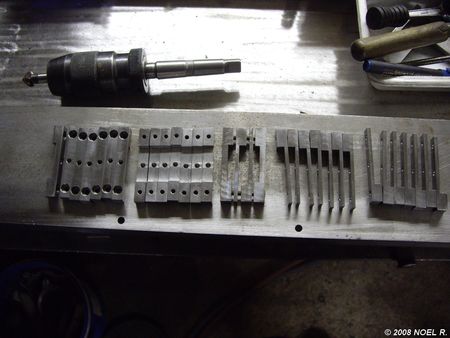
Voici toutes les pièces finies .
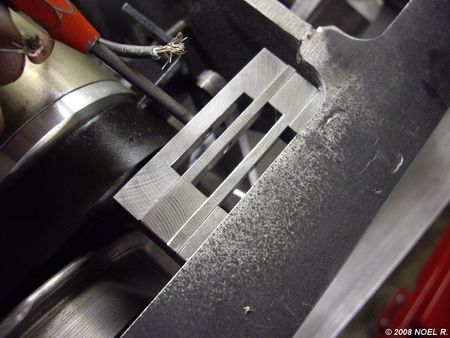
Ce support pendra place sur le flanc intérieur du bogie .
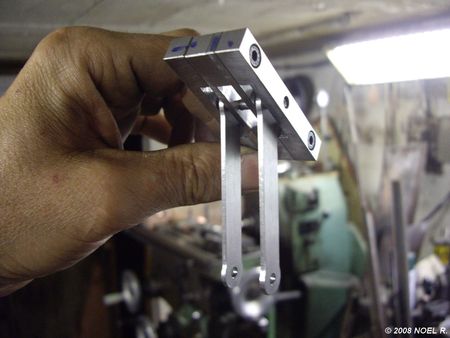
Voici les deux biellettes en place dans le support .
Les sabots de frein .
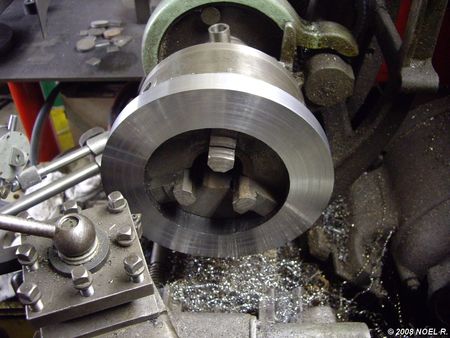
Tournage de la bride qui va servir de point de départ pour la réalisation de huit sabots de frein .
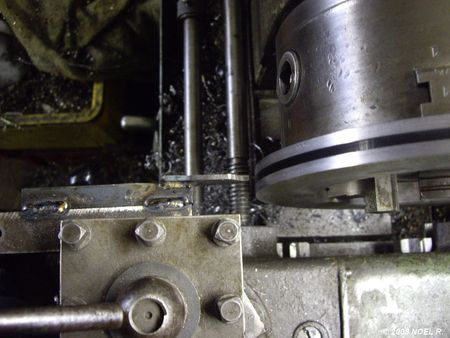
Je suis un peut hors capacité du tour et il faut faire un outil déporté pour la saignée .
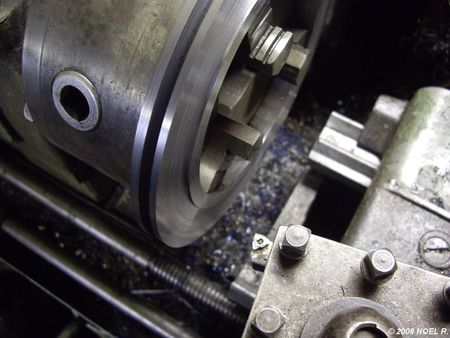
Tournage d'un épaulement pour figurer la jonction entre le sabot et son support .
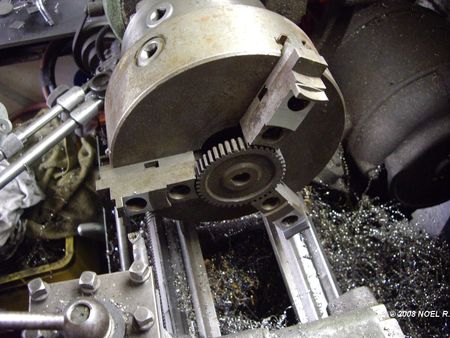
Alésage des mors doux pour faire la reprise conique du centre de la couronne .
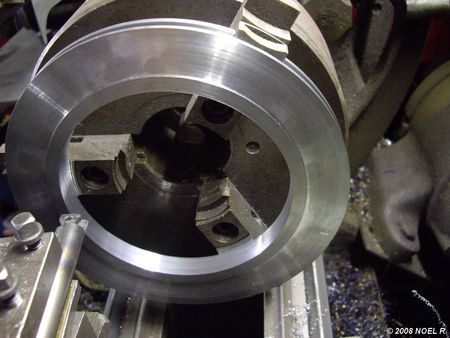
L'alésage est fait à un angle de 2° comme sur les roues .
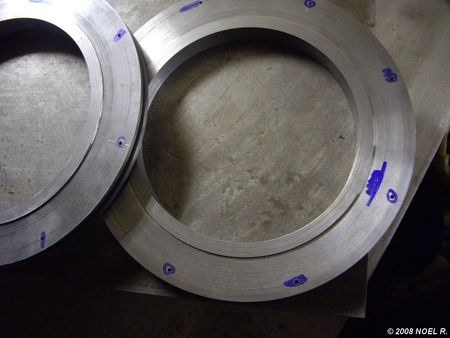
Pointage et perçage des tous d'axe de chaque sabot .
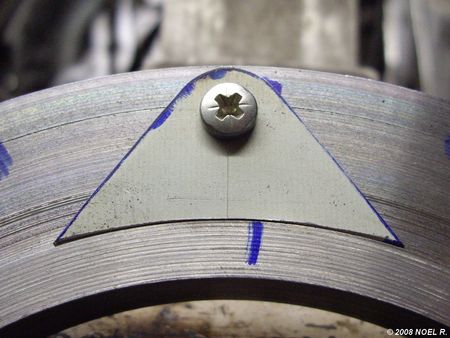
J'ai fais un petit gabarit en tôle pour faciliter le traçage du profil de chaque pièce .
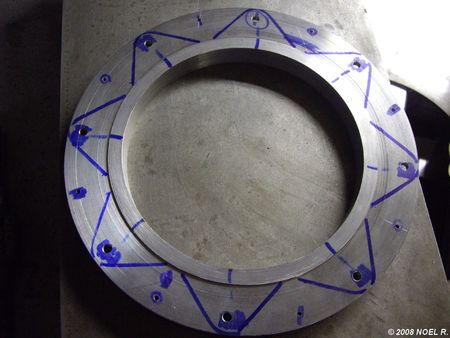
Le traçage est fait .

Le surplus de matière est enlevé par fraisage en suivant le trait , une grande précision n'est pas requise ici .
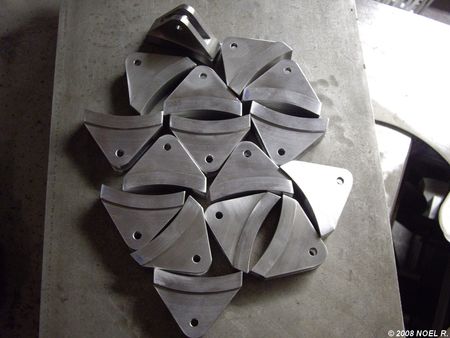
Après avoir scié les pièces entre elles et fraisé les bouts , nous voici en présence des 16 sabots qui vont équiper le Yaya .
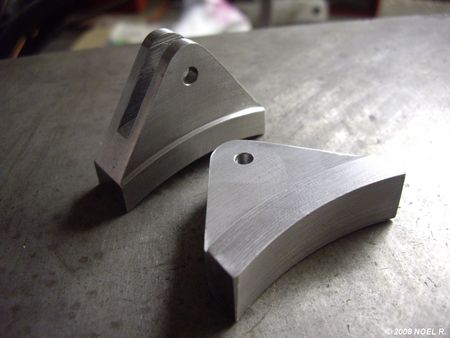
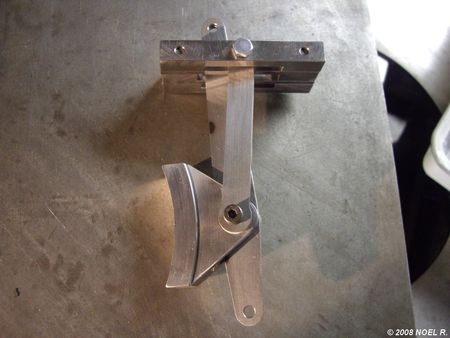
Voici comment s'articule le balancier et ses biellettes .
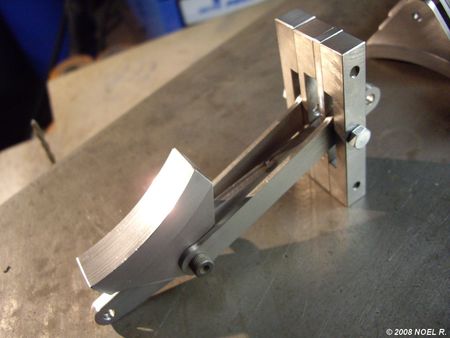
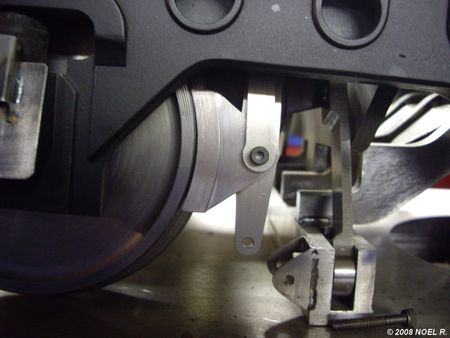
Une fois monté ça ressemble à ceci pour les sabots centraux .

Et ceci pour les sabots externes .
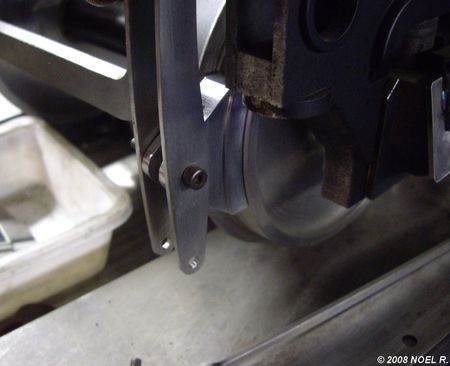
Les balancier de freins externes sont doubles , il n'y a rien de simple sur cette machine !
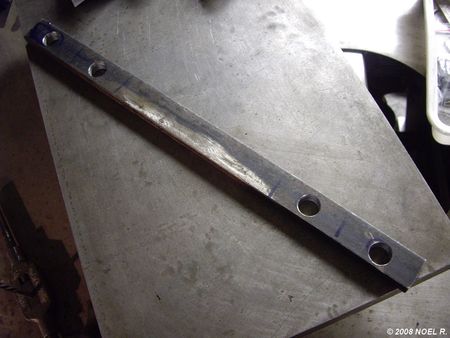
Les paliers supports des balancier externes sont fait en mécano-soudure .
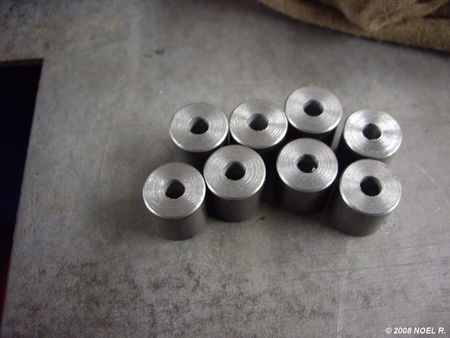
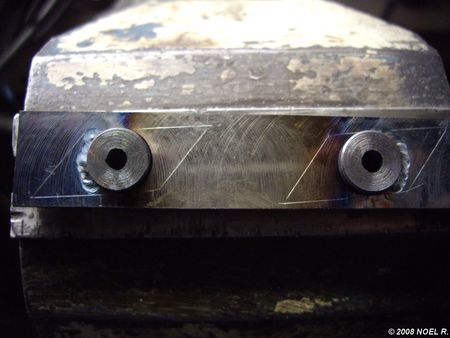
Seulement un côté du rond est soudé , une fois détaché l'autre partie du plat servira à une autre pièce .
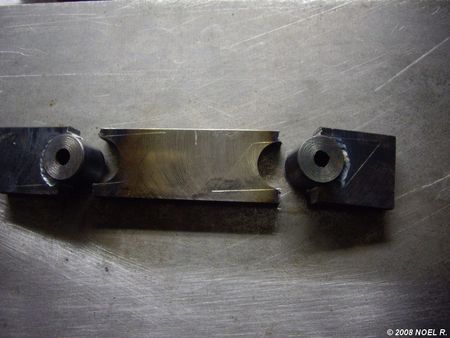
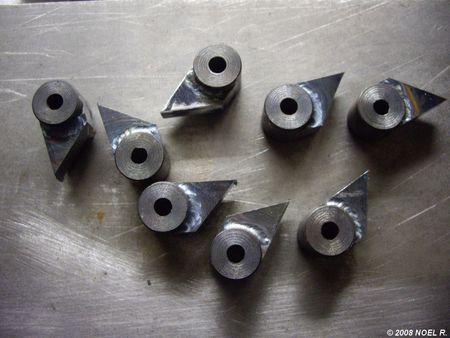
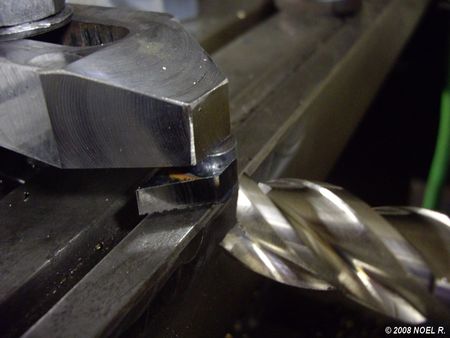
Le fraisage est fait en suivant le trait .
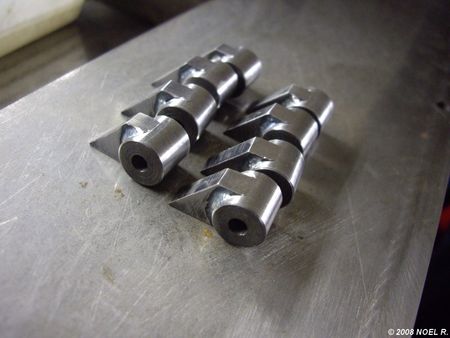
Les paliers sont prêts à être soudés sur le châssis du bogie .
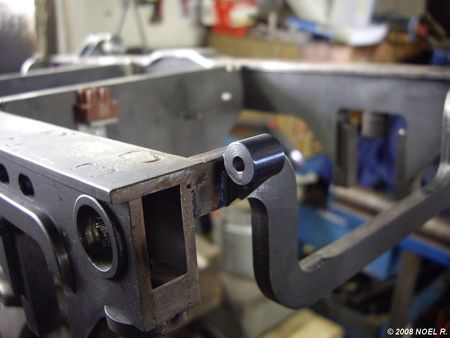
Ils sont soudés en place par un cordon au tig de chaque côtés .
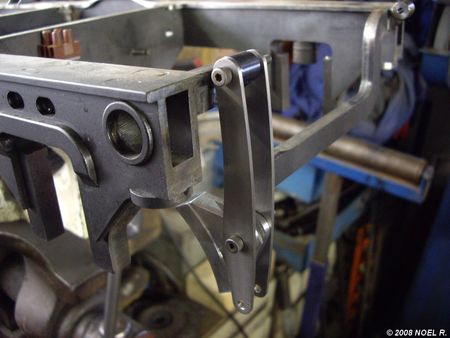
Montage à blanc ds balancier sur les paliers .
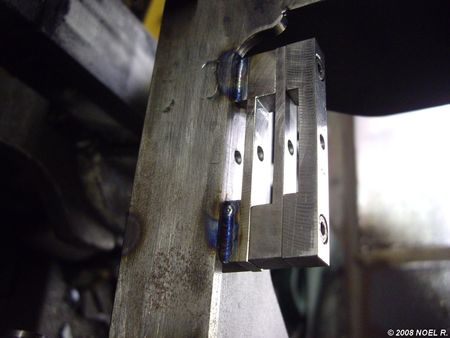
Les supports de balanciers internes sont soudés aussi au tig avec un cordon dessus et dessous .
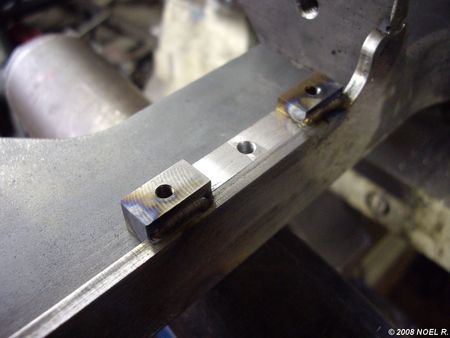
L'échauffement du métal est minime (couleur bleue) et cela n'entraine que peu de déformations des pièces.
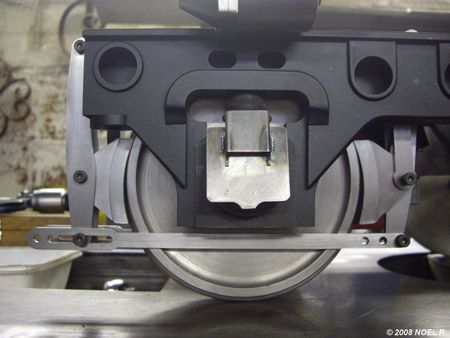
Montage à blanc de la tringlerie pour vérifier les côtes .
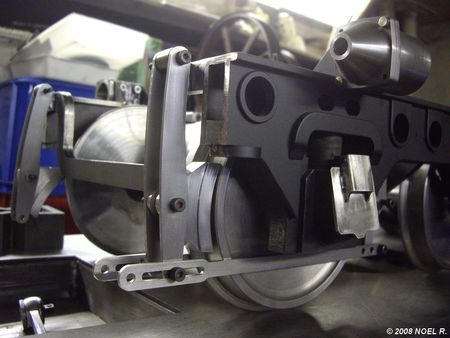
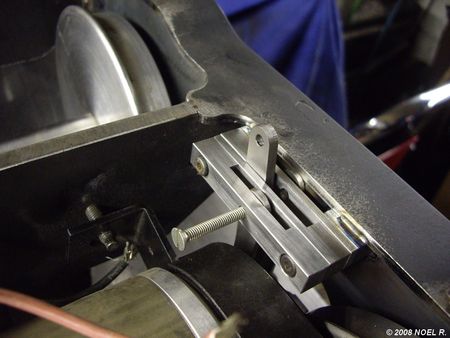
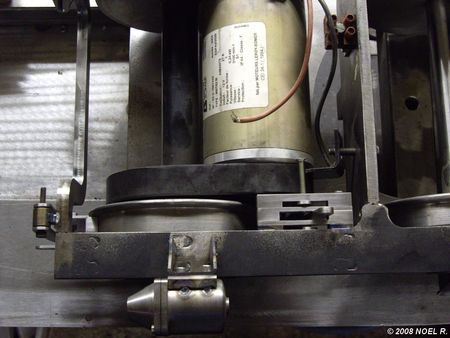
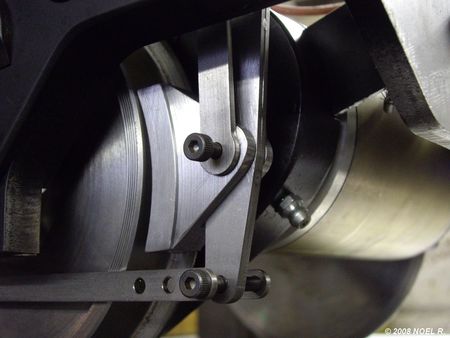
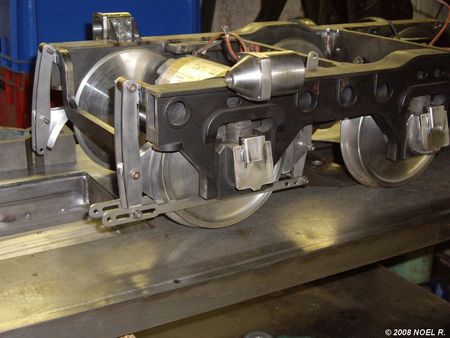
Il reste encore du boulot mais ça commence à prendre forme .
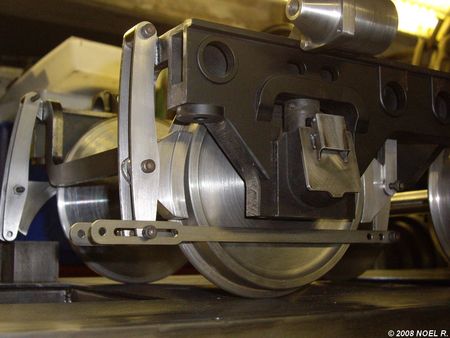
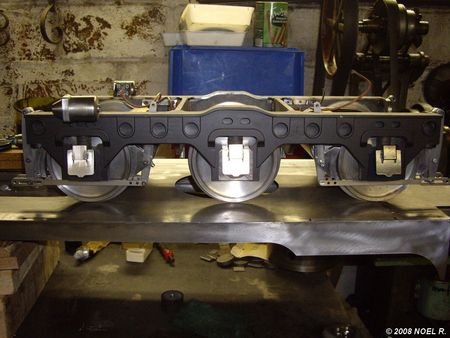
Les glissières de palonnier.
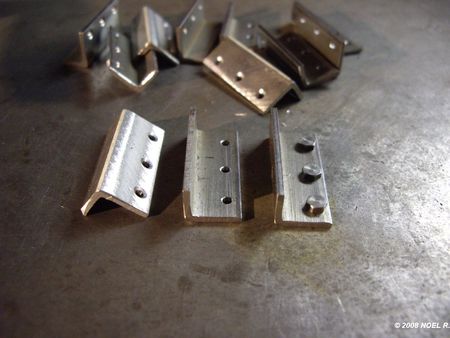
Ces petites cornières sont tirée d'une chute de tube carré . Les fausses vis de fixation sont serties par l'arrière en repoussant le métal .
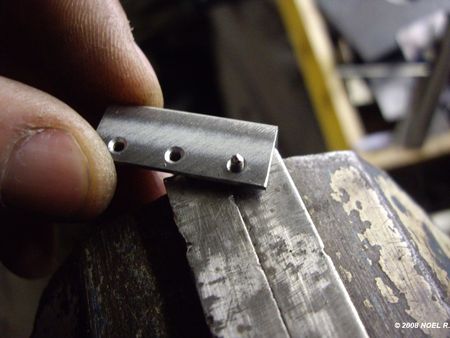
Comme pour un rivetage affleurant la tige est matée dans la fraisure .
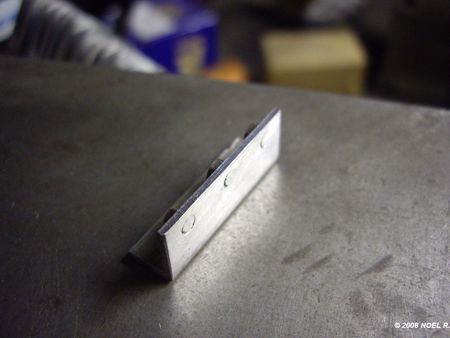
Ensuite on donne un coup de lapidaire pour retirer le surplus de matière et la face est bien plane .
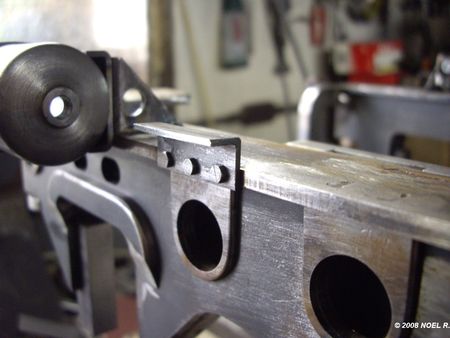
La cornière est soudée par l'arrière sur le bogie .
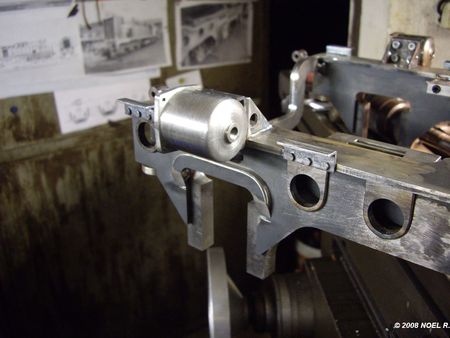
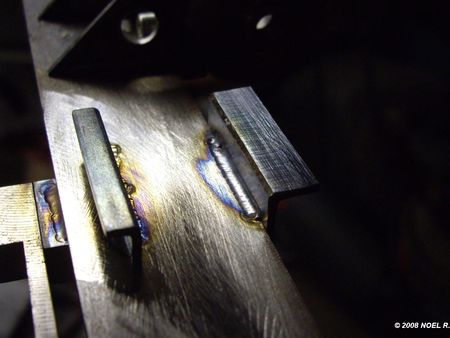
Une deuxième cornière est soudée pour supporter le palonnier .
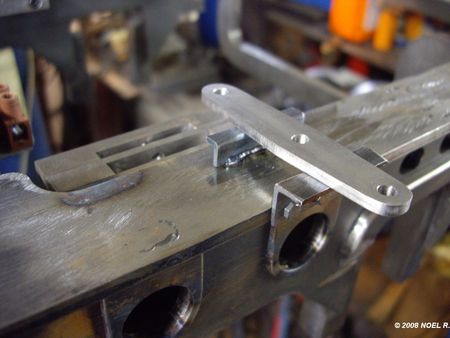
Le palonnier est fait dans de la tôle de 3 mm .
Mon vieux lapidaire à rendu l'âme !!
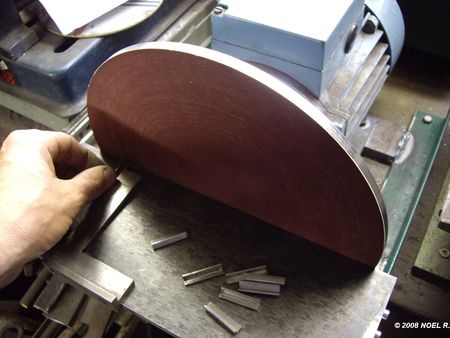
Le lapidaire que j'avais fait avec un moteur de machine à laver a décidé de ne plus fonctionner, j'attendais ce moment pour le remplacer par un modèle plus grand .
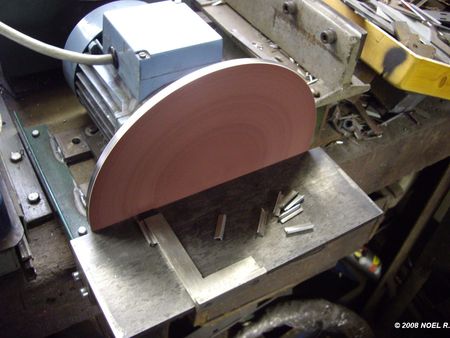
En effet je vien d'en refaire un avec un plateau de diamètre 270mm (160 pour le précédent)
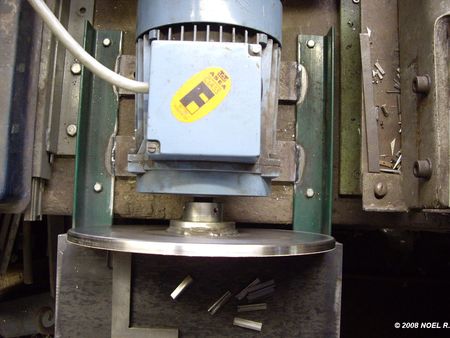
C'est un montage simple réalisé sur la base d'un moteur de 1cv triphasé qui tourne à 1400tr/min.
Les manilles .
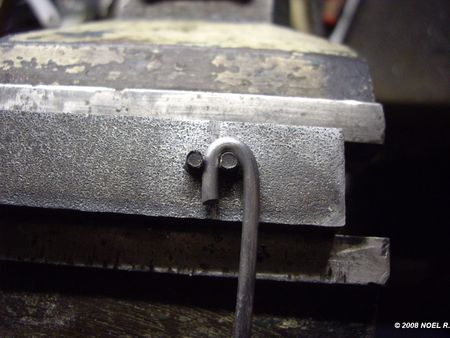
Le corps de la manille est fait avec du rond de 3.2 mm (âme de baguette à souder). Il est cintré entre deux griffes .
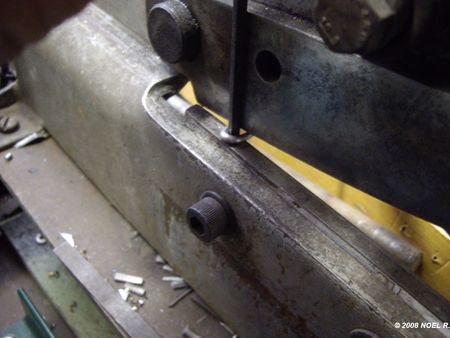
Le U est cisaillé en prenant un morceau de fer plat comme guide de profondeur .
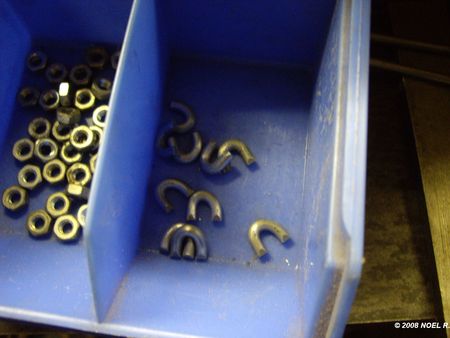
Prêt pour la soudure , les U d'un côté et les écrous M4 de l'autre .
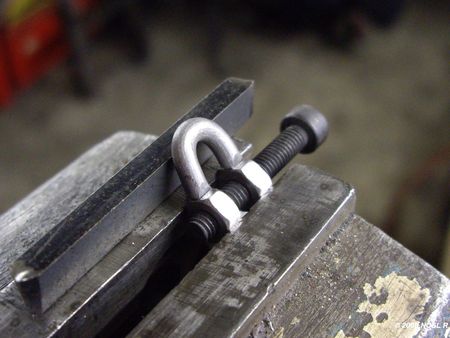
Les écrous sont maintenus aligné au bon entraxe sur une vis .
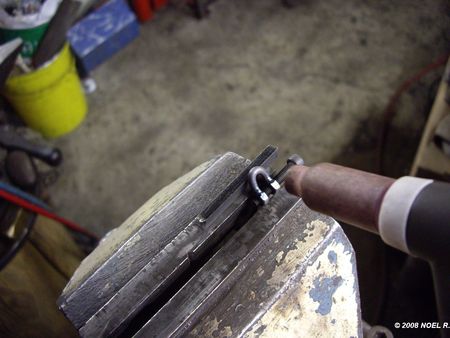
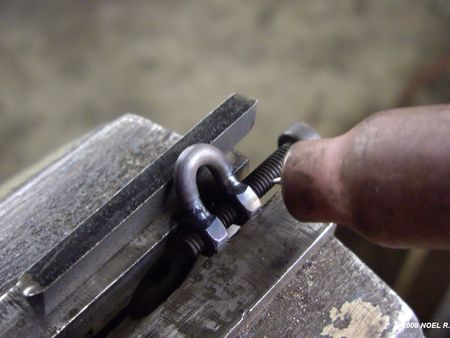
Soudure des U sur les écrous .
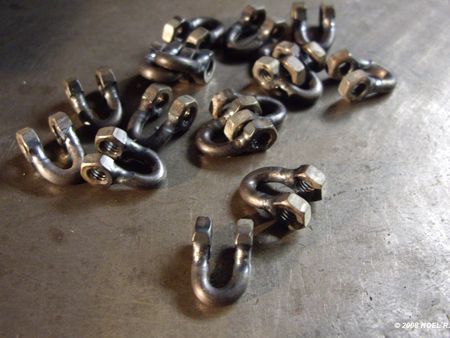
Il en faut des manilles !
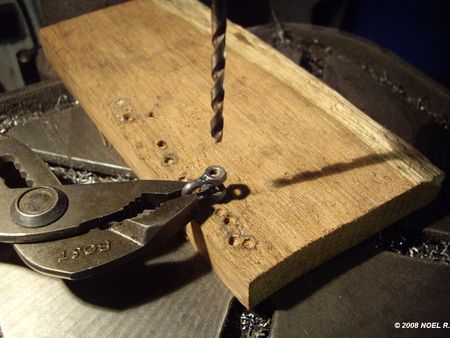
Perçage des trous au diamère 4 mm .
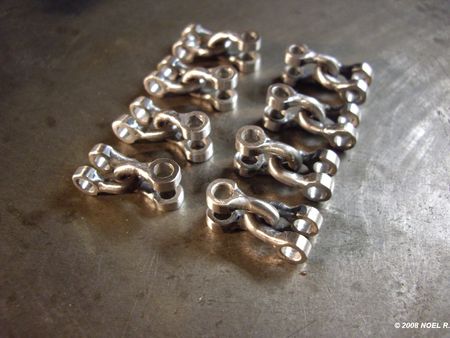
Les facettes des écrous sont arrondies au lapidaire et les manilles sont terminées .
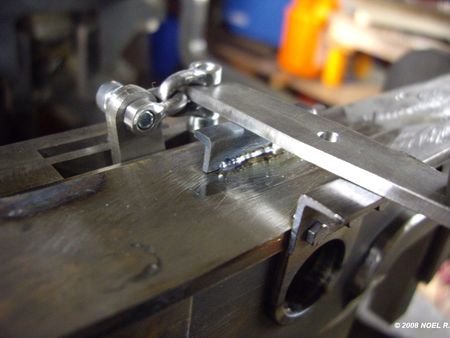
C'est ici que prennent place les manilles .
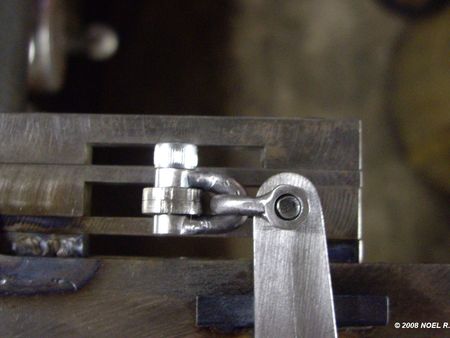
La même en vue de dessus .
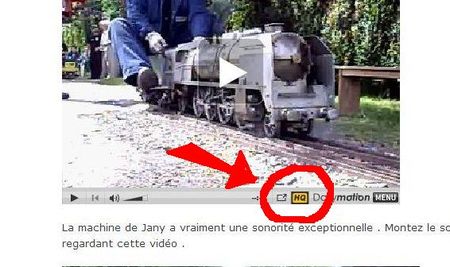
Dailymotion change d'encodage et ça se voit!
N'hésitez pas à revoir les vidéos du blog en cliquant sur la case HQ pour profiter d'une qualité d'image améliorée ( enfin cela reste quand même des vidéos prises avec un appareil photo ! )
Les tirands de commande de frein.
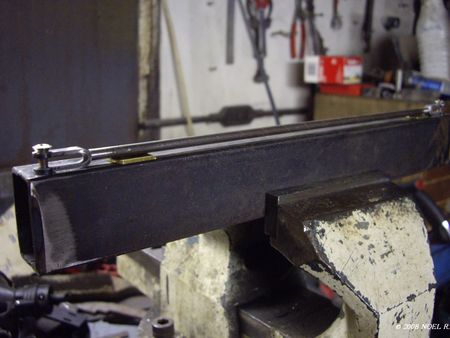
La timonerie de freinage est reliée d'un essieu à l'autre par ces grandes chapes que nous allons réaliser en trois parties soudées entre elles . L'extrémité de la chape est faite dans de la tôle de 2mm et l'axe dans du rond de diamètre 5 mm.
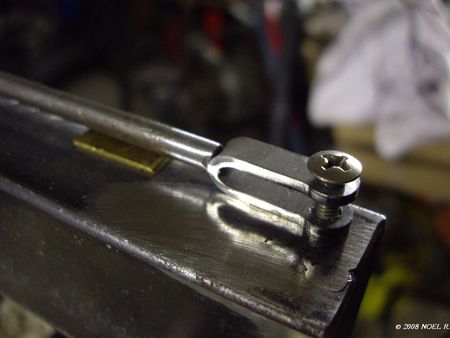
Les chapes sont vissées sur un support au bon entraxe pour qu'elles se tiennent bien pendant la soudure.
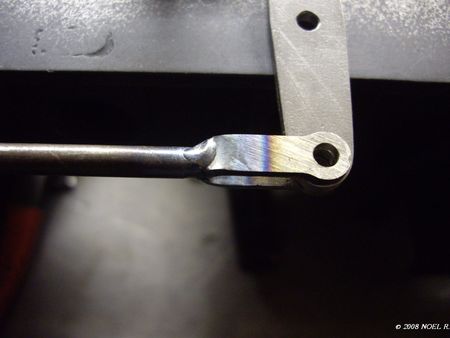
La soudure n'est pas parfaite mais la peinture cachera la misère .

Voila , c'est ici que la tringle prend place .
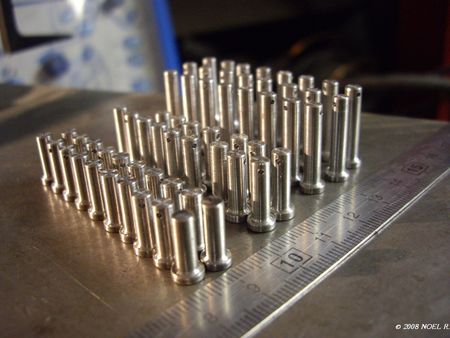
Toutes ces chapes , balanciers , sabots de frein , etc., etc. ... vont nécessiter des axes pour faire la liaison de tout ce joli petit monde , et bien c'est chose faite . C'est là que je me dis que j'aimerai bien avoir un tour à décolleter pour aller plus vite , ce n'est pas gros comme pièce mais ça prend un temps fou .
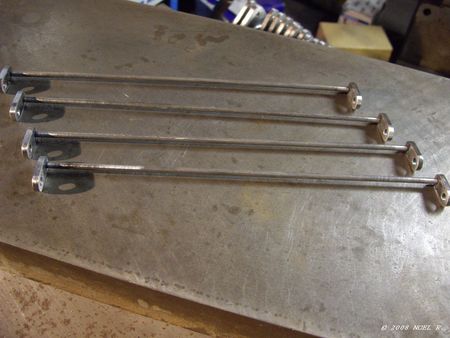
Des tiges de rappel sont placées entre les sabots de frein extérieurs pour ne pas qu'ils s'échapent de la bande de roulement lors du freinage. Celle-ci étant conique , les sabots on tendance à partir vers l'extérieur en glissant sur la pente .
Les chapes sont faites dans de la tôle de 3 mm et les tiges dans une âme de baguette à souder de diamètre 3.2 mm .
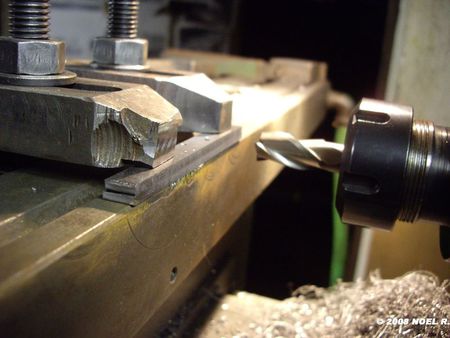
Dressage de deux morceaux de fer plat de 3x10 pour faire des platines de 8x8 .
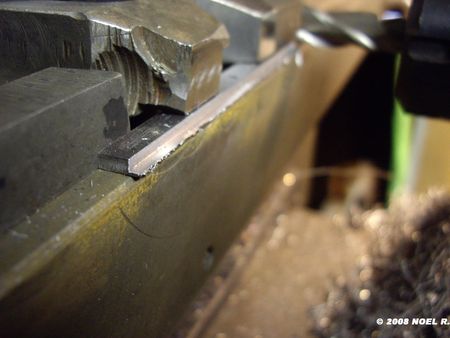
Un épaulement de 2 mm est fraisé de chaque côté .
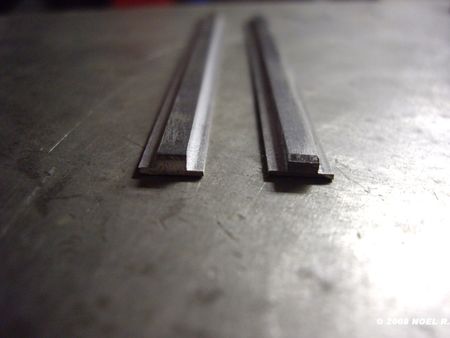
Voici nos deux barres en T .

Perçage d'un trou de diamètre 4 mm avant de scier la première pièce et ainsi de suite pour les suivantes . Après sciage les extrémitées sont dressées au lapidaire.
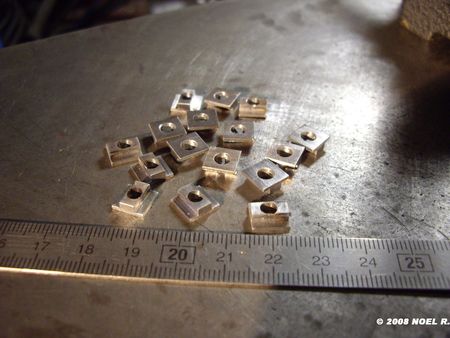
Comme il en faut 16 et bien les voila .
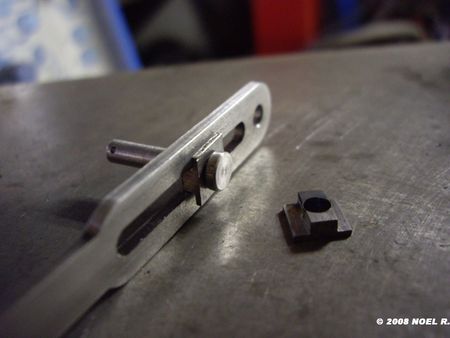
Montage à blanc pour voir .
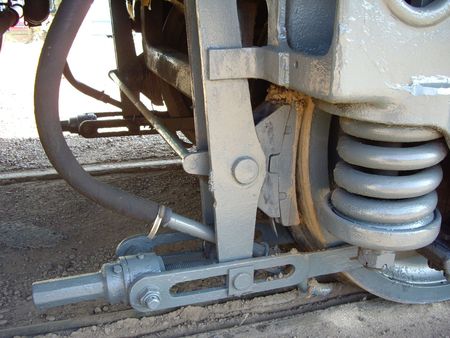
Je vais maintenant passer au dispositif de réglage du jeu de la timonerie de freinage . Il sera fictif tout en préservant l'aspect extérieur .
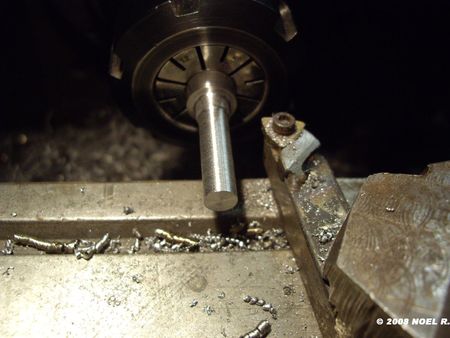
Tournage des épaulements dans du rond de 12 mm.
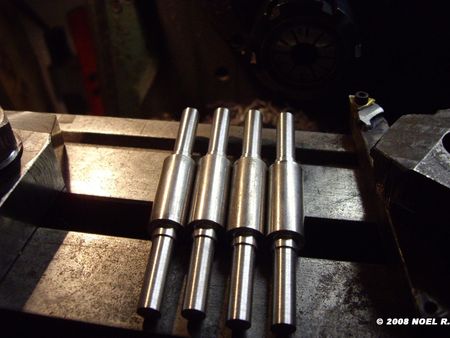
les pièces sont faites en symétrie .
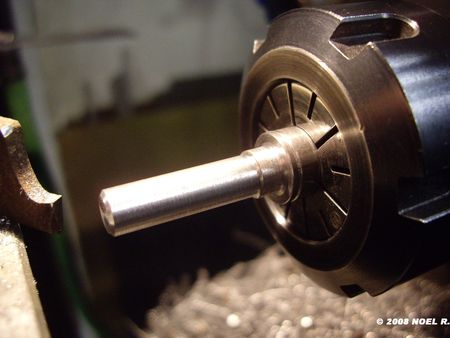
Chanfreinage du bout et matquage de la sépatation fictive entre deux pièces (à droite).
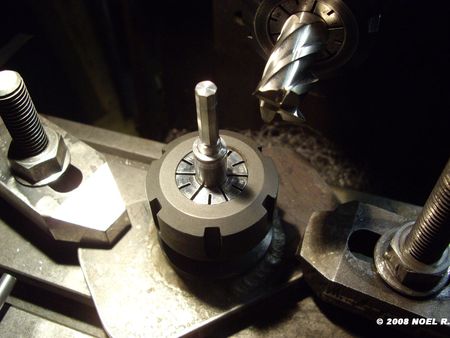
Fraisage du huit pans dans le montage en pince .
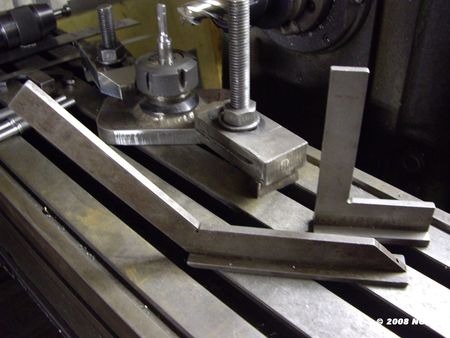
Le montage est dégauchit successivement avec l'équerre à 90° et à 135°.
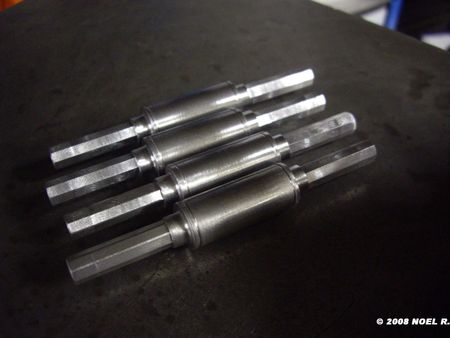
J'ai du faire la partie octogonale un peu longue , je vais la rependre . J'aurais du prendre le temps de faire un plan de la pièce et ne pas taper dans la masse juste en regardant une photo de la pièce originale . A vouloir aller trop vite on ne gagne pas toujours !
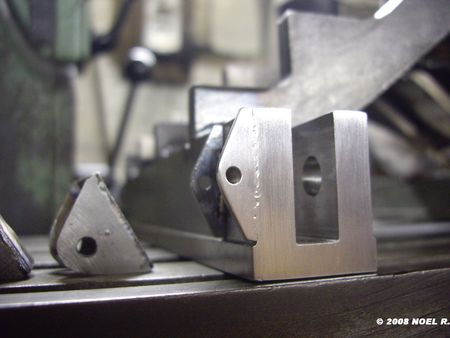
La forme des chapes des traverses dansantes n'était pas tout à fait conforme et comme cela ne me convenait pas je les ai refaites à la bonne taille , on voit à gauche la pièce qui a été déssoudée .
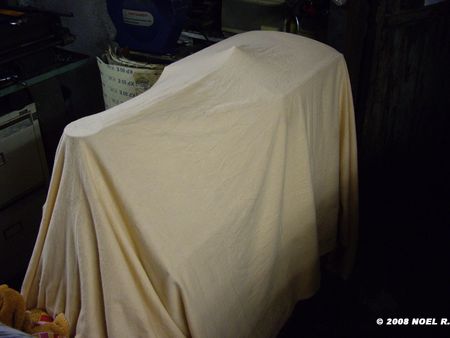
Voici des nouvelles de la Decau, elle à fait le plein de liquide anti-gel dans la chaudière et à revêtu son manteau d'hiver en attendant avec imptatience le début de la saison prochaine au mois d'avril 2009 sur les voies du PTVF .
0
0
0
0
0